How We Test Tires
One of the ‘secrets’ behind the performance of Rene Herse tires lies in our R&D. We run our tests under real-world conditions, so we can optimize our tires for what matters: riding on real roads. When we started our research 15 years ago, high-performance tires were narrow and designed for high pressures – because that’s what makes tires fast in lab tests. In other words: The way a company tests performance determines how that company makes its tires. If the tests aren’t realistic, the performance of the tires will be compromised in the real world—where it matters.
That’s why our real-road tire tests were so ground-breaking. We found that high pressures don’t make tires roll faster. That wide tires can be as fast as narrow ones. And that a supple casing is the most important requirement for a fast (and comfortable) tire. Back then, that was revolutionary. There were no tires that met these requirements—so we started making our own. Now other companies are also offering wide tires designed to roll at low pressures, but we don’t know of any who test their tires under tral-world conditions with a rider on the bike.
Performance testing of tires is complicated because it goes to the heart of the interactions between rider, bike and road surface. In fact, misconceptions about tire performance have persisted for so long because testing tires is so difficult. Even car tire makers, with multi-million-dollar research budgets, got the science wrong. When the Toyota Prius (one of the first hybrid cars) was introduced, its tires used an extra-hard rubber compound. This offered poor grip, but was thought to improve efficiency. Only recently have car tire makers discovered that tires made with softer, grippier rubber transmit fewer vibrations and are more efficient on real roads than harder tires that perform well in lab tests.
Let’s look at how tires affect the performance of a bike:
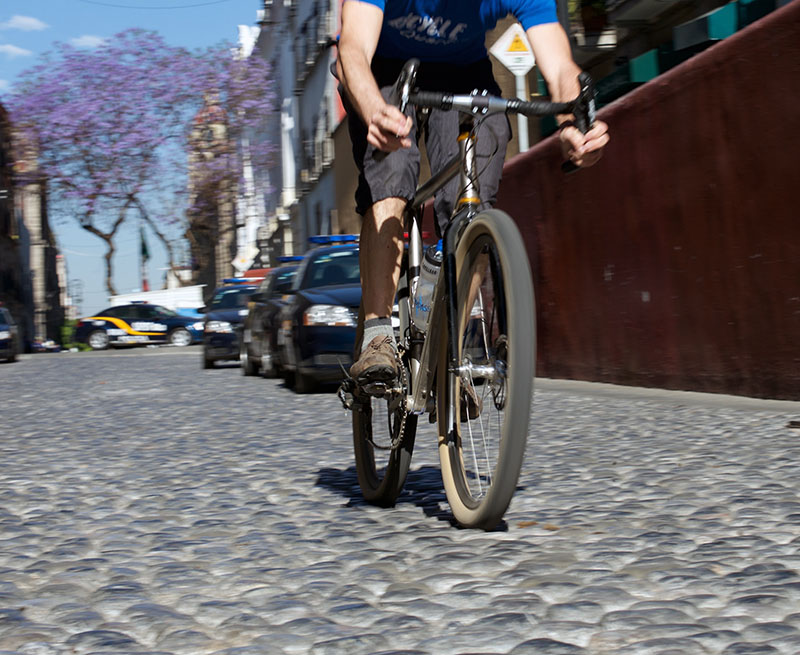
Two factors influence the rolling resistance of the bike. One is well-known, the other is often overlooked. Looking at the photo above, you can envision these two factors.
Energy absorbed in the tire as it flexes (hysteresis losses)
As the tire rotates, it flattens at the bottom. This takes energy – imagine squeezing a tennis ball. The less the tire flexes, the less energy it will absorb. Higher tire pressures and harder rubber make the tire flex less. That’s why all of us used to think that tires rolled faster if we made them from harder rubber and inflated them harder. But this overlooked an important factor:
Energy absorbed by rider and bike (suspension losses)
As bike and rider vibrate, energy is lost to internal friction in the bike and especially the rider’s body. What we experience as discomfort is actually friction between the tissues of our bodies. (In cars, the same losses occur mostly in the shock absorbers.) The technical term for this is ‘suspension losses’ (sometimes also called ‘vibration losses’). These losses can be very high. One Bicycle Quarterly test found that riding on a rough surface required 490 watt more than riding on a smooth road. Both roads were flat; the bike was the same, nothing had changed except the road surface—the 490 watt difference was entirely due to the higher suspension losses on the rough road.
Even on smooth roads, suspension losses are significant. That’s why we use pneumatic tires: The air in the tires is essential to reduce the vibrations and the suspension losses, but this doesn’t work well if we inflate our tires too hard.
We found that these two factors—flex in the tires and vibrations—act like a see-saw: If we inflate our tires harder, we decrease the flex (hysteresis losses) in the tires. At the same time, we increase the vibrations (suspension losses). The net results is that we haven’t gained anything. If we think of energy loss as heat generation, high pressures mean that our tires stay cool, but our bodies get hot. If we only measure the tires, it appears that higher pressures (and harder rubber) save energy. But when we look at the entire system, we realize that those gains have been offset by losses elsewhere.
This is also why supple casings offer such a huge performance benefit: They reduce the hysteresis losses in the tire—imagine squeezing a soft foam ball instead of a hard tennis ball—and they absorb vibrations better, so they reduce the suspension losses, too. Racers have known for almost a century that supple casings make tires fast, but lab tests couldn’t show how great the benefit really was. That is why tire makers focused on tread rubber compounds and other ‘magic’ formulas, when the casing matters so much more.
To truly evaluate the performance of tires, we need to look at the entire system. That’s why we developed new tire testing methods to get accurate measurements of how tires affect a the performance of the entire bike.
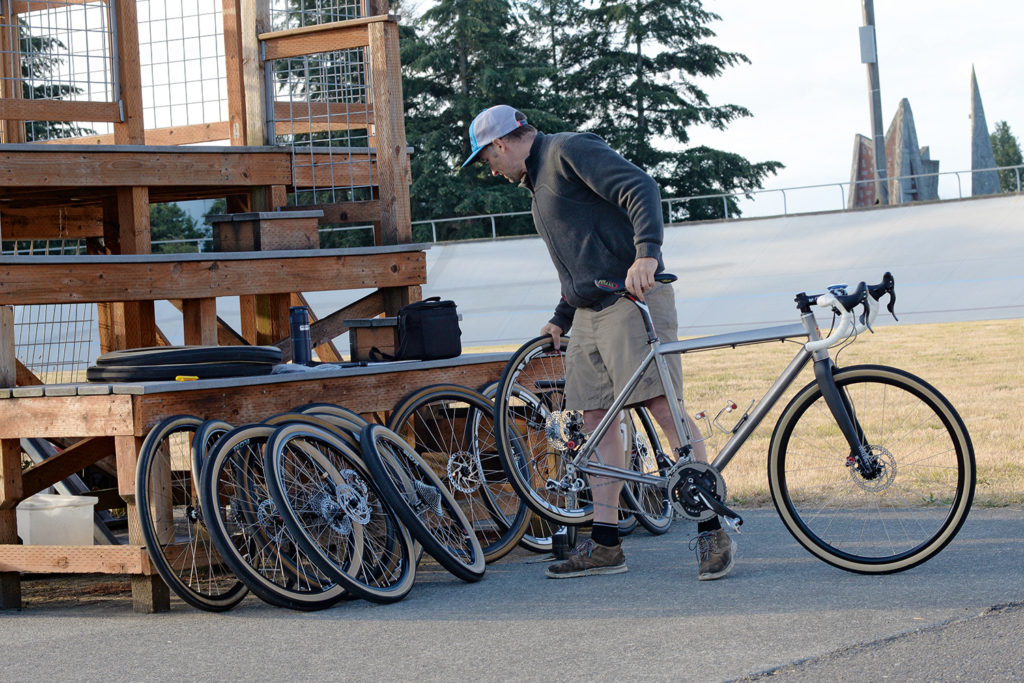
Real-Road Testing
The only way to test the entire effect of different tires on a bike’s performance—both hysteresis and suspension losses—is by testing with a rider on the bike. Testing tires on real roads has revolutionized our understanding of tires. We found that higher pressures don’t roll faster (see above). We also found that wide tires don’t roll slower than narrow tires—at least in the size range that we ride on our all-road bikes (25-55 mm). And we found that a supple casing has a greater influence on tire performance than previously thought.
Over the last 15 years, we’ve refined our methodology. Our first tests were great for finding relatively large differences between tires—like the speed advantage of 25 mm tires over the 23s that all racers used back then. (When we shared our results with a technical consultant of a pro team, it got the ball rolling, and soon that team moved to wider tires, and then others followed in due course.)
It got a bit more complicated when we found that there was no significant speed difference between tires as wide as 54 mm and as narrow as 25 mm (with the same supple high-performance casings). What does ‘significant’ mean? With our early tests, if there was a 1% speed difference, we would not be able to determine this. And yet going 1% faster over a 200-mile race can make a difference of 6 minutes at the finish! You wouldn’t want to ride 54 mm tires if 25s would get you to the finish six minutes faster—or vice versa!
So we’ve refined our methods to pick up smaller and smaller differences. Another way to increase our confidence in the results was running more tests with different methodologies. They all showed the same results: Supple tires are faster. Wider tires aren’t slower. High pressures aren’t needed for performance. That way, we gained more confidence in these results.
Why doesn’t everybody tests on real roads? Real-road tests require a huge amount of effort – not in equipment, but in time. You can’t just test on any given day – you need perfect conditions with no wind and constant temperatures. We usually test just before sunrise, when there’s the least amount of air movement. In Seattle, we test during the summer months, because that’s when it’s often calm. It’s not really feasible for a big tire company to wait six months, then send their engineers to a hill at 5 a.m., finally ready to test, only to return to the office empty-handed because a very light wind has sprung up. You have to be somewhat crazy to do this, but it’s the only way.
Well, almost: We’ve often dreamed of buying an old railroad tunnel, outfit it with different surfaces from smooth pavement to rough gravel, and test there. Inside a tunnel, there would be no wind and constant temperature. In fact, this idea isn’t as crazy as it sounds: The British car industry uses such a tunnel for their testing.
More seriously, let’s look at the pros and cons of some popular testing methods.
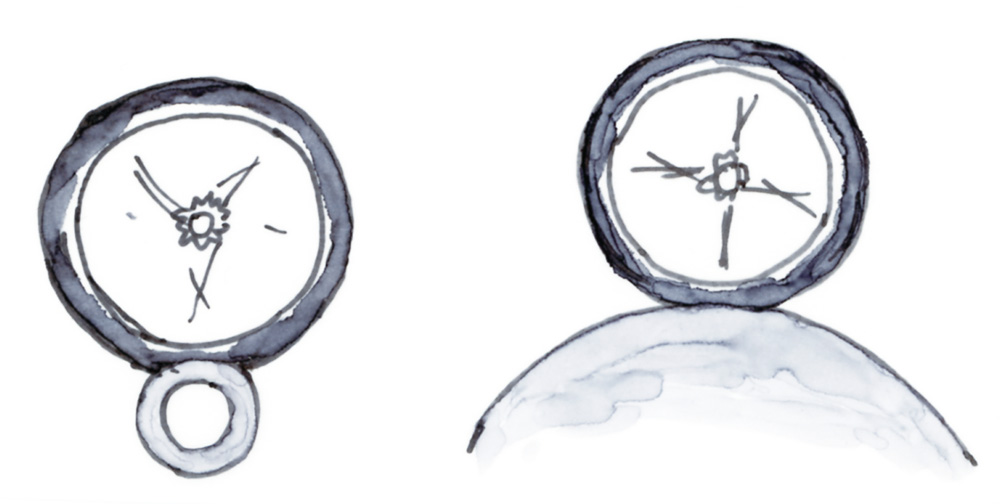
Drum Tests
The classic way to test tires is on a big drum that simulates the road surface. The power required to spin the drum empty is measured, then a wheel with a tire is added to the setup. A spring or shock absorber pushes the tire onto the drum with a force that equals the load of bike and rider. The power required to spin the drum is measured again, and the difference is how much energy the tire absorbs as it rolls over the drum.
Apart from the fact that we don’t have a rider, so we can’t measure suspension losses, steel drums have another problem: They are convex, so they press deeper into the tire than a flat road (left). That effect is more pronounced with supple tires than with stiff ones. This means that supple casings deform more on a steel drum than on a real road – which exaggerates their hysteresis losses. Supple tires still perform better on a drum than stiff tires, but their advantage is much smaller than on real roads. In other words, the casing makes relatively little difference in a drum test, but it makes a huge difference on the road.
For the same reason, low pressures make a tire much slower on a steel drum—the drum presses deeply into the softer tire. And yet on real roads, running your tires softer doesn’t slow you down. (Until the tire gets to soft that it becomes almost unrideable.)
A solution is to make the drum very large (>1.8 m/6 ft), but this gets very expensive——and you’re still not measuring the suspension losses. Basically, steel drum tests tell you to make your tires stiffer and to use higher pressures—but things doesn’t work that way on real roads.
In summary, supple tires perform well on real roads, but they don’t test well on steel drums, because:
• supple tires deform more at the same pressure
• the concavity of the drum presses into supple tires more
• suspension losses aren’t measured on steel drums
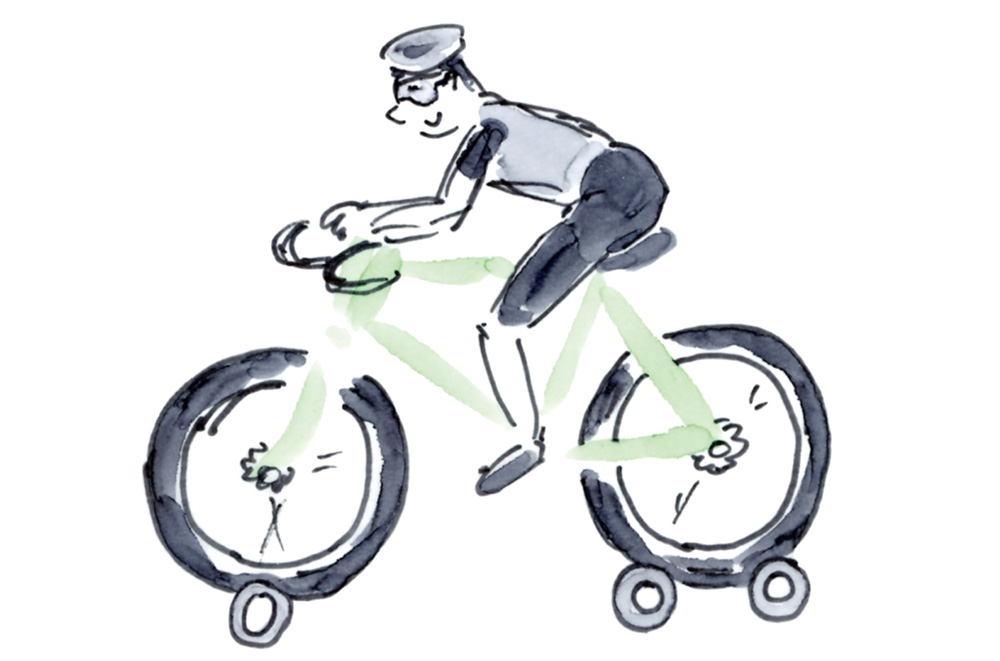
Roller Tests
What if we put a bike with a rider on the steel drum? We could make the steel drum rough to simulate real pavement, too… To keep a bike stable on steel drums, we need three, like the rollers used for indoor training. This limits the size of the drums: They have to be quite small, which makes them more convex (with the problems described above). If we use a commercially available roller trainer, the drums are very small, and the effect of the rollers pressing into the tires is magnified. We can feel this effect: When we stop pedaling, the rollers quickly stop, whereas we coast for a long time on a real road.
In theory, it is possible to mathematically correct for the effect of the roller’s convexity, but the correction factor will be different for tires with different stiffness. To get accurate correction factors, we have to measure the performance of our tires on a real road first. So we end up with a chicken-and-egg problem: For each tire, we need accurate test results to determine the correction factor that will give us accurate test results.
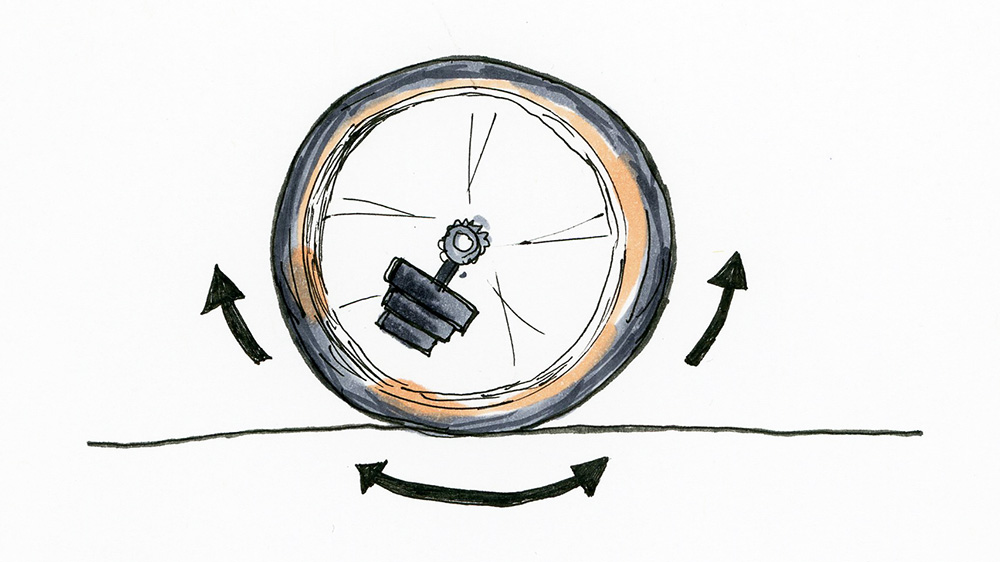
Pendulum Tests
TOUR magazine in Germany came up with a rather ingenious test for tire resistance: They built a pendulum that rolls back and forth on a simulated road surface. The pendulum moves at low speed, so wind resistance isn’t a major factor. The road surface is flat, so there’s none of the pressing into the tires that you get with convex drums or rollers. TOUR measures how long the pendulum swings, and from that they calculate the energy consumed by the tire (and hence the rolling resistance).
The speed isn’t constant, of course, which introduces a flywheel effect with heavier tires. So you’ll want to equalize the weight of the tires by adding weight to the rims. This seems like a promising way to test the hysteresis losses caused by the deformation of the tire. Of course, you still don’t measure the suspension losses—for that, you need a rider on the bike.
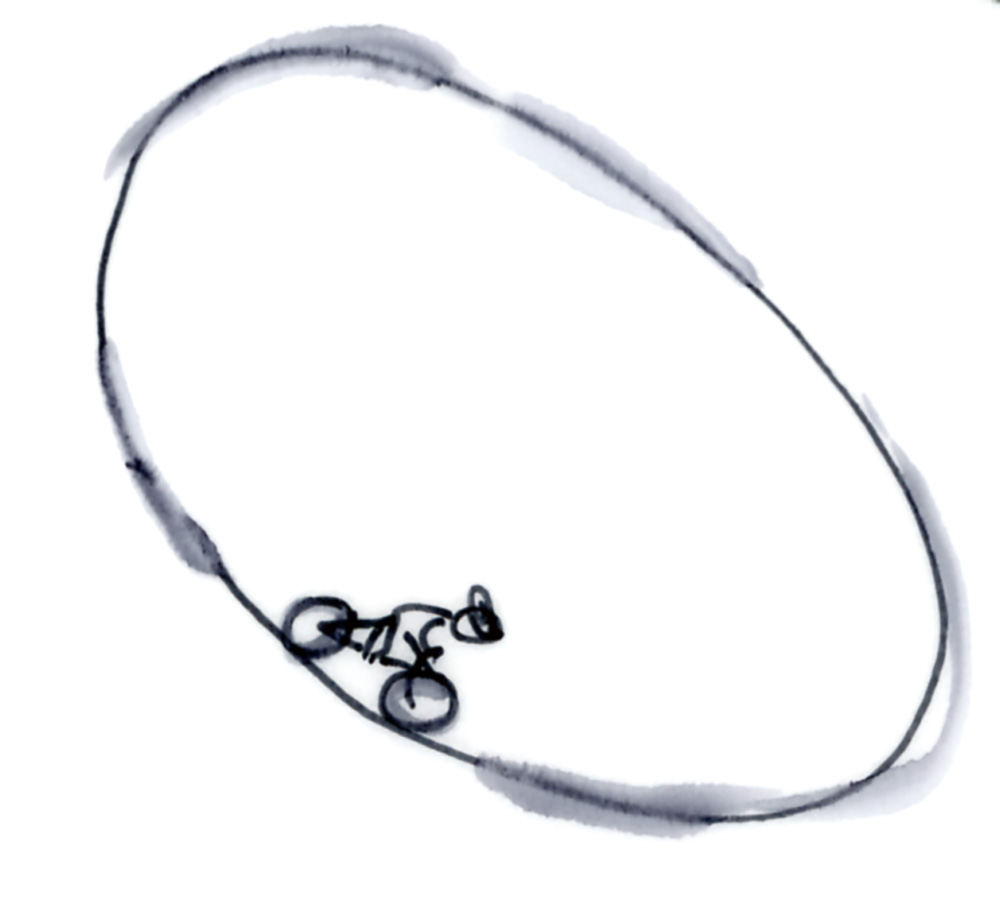
How to Design Real-Road Tests
So that brings us back to real-road testing. By using a real road, a real bike and a real rider, we are making sure that the system’s three most important parts are present. The problem is that we also have to deal with many other variables, especially wind, temperature and rider position. To get meaningful results, we need to keep these factors as constant as possible. Only our tires should change from one test run to the next – but not wind, temperature, rider position, etc.
We’ll test on a completely calm day, because wind is never uniform—it’s always associated with gusts. Even very slight variations in wind speed will affect our results. Because rubber softens as it warms, the temperature must be as constant as possible. (It is possible to correct for temperature changes, but this introduces another variable.) The rider must be able to maintain the same position for dozens or hundreds of test runs. (We’ve confirmed in wind tunnel tests that our tester can get into the same position time and again…) And the road surface must be relatively uniform. If the rider pedals, the test surface must be perfectly flat, because pedaling even just slightly uphill requires more power than pedaling downhill, and one requirement for a good test is a constant power output.
The better we control all these conditions, the better our results will be. It may be tempting to test on a day when there is almost no wind, or to use a test track that is almost flat, but we’ll introduce more and more noise. It doesn’t take much before we can no longer discern small differences between tires. In the end, our statistical analysis (below) will tell whether we’ve been successful or not.
When all these requirements are met, tires can be tested reliably on real roads. With a rider on board, there always will be more noise than in an optimized lab setting. This means that more test runs are required to detect small differences between tires. Very small differences may be undetectable because testers run out of time before conditions change. Our goal is to fine-tune our tests so that we can detect meaningful differences. If one tire is 1% faster than another, we want to detect this. If the tire is 0.1% faster, we cannot detect this, but it doesn’t matter: It won’t change how we ride. (In any case, there is always some variation between tires of the same model due to the tolerances of manufacturing.)
For testing with a power meter, a circular test course helps with time-keeping. However, pedaling always introduces noise, because it’s difficult to keep the power output constant. We’ve used tests at the velodrome to validate the results of our roll-down tests (below). The same tires were fast and slow in both tests; high pressures didn’t make the tires faster, etc. This gave us confidence that there wasn’t some—potentially undiscovered—systemic flaw in our roll-down tests.
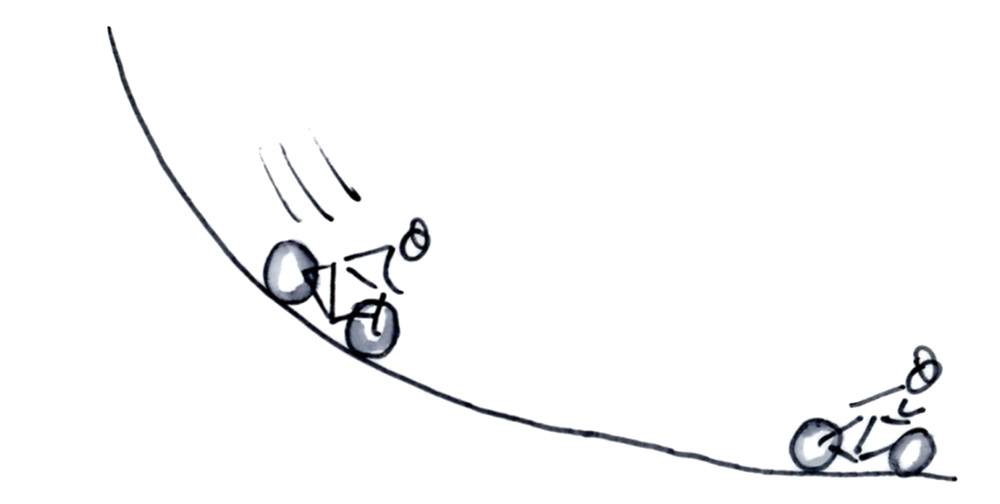
Roll-down tests remove pedaling from the equation: Gravity is a constant, so the energy input into the system does not change. A coasting rider is better able to maintain the same position. And we don’t have to worry about the variability that is inherent in power meters.
The best roll-down tests are done on a constant slope, at the ‘terminal speed’ that the rider reaches when the bike no longer accelerates. A steady-state system has fewer variables than a ‘roll-out’ on a hill that ends in a flat road, where the rider slows down at the end of the test. (Wind resistance changes dramatically with different speeds.)
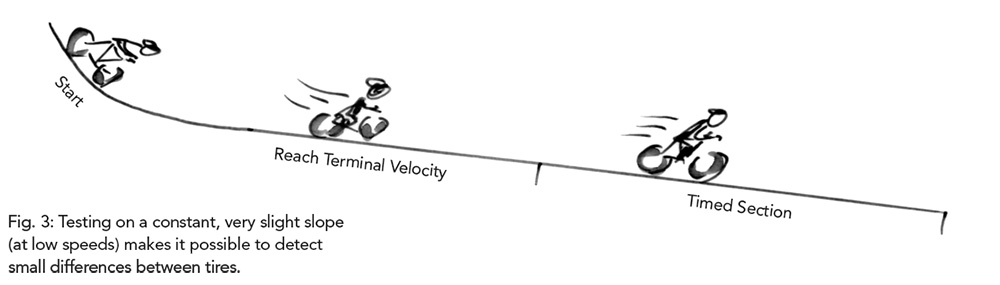
Finding the right hill is another difficult task. You want a hill that’s steep at first, so you get up to speed quickly. (Otherwise, you’d need a very, very long hill.) After that, you need a long stretch with a constant gradient, where the rider reaches a constant velocity. Then comes the timed section, which should have the same gradient, so the speed doesn’t change. The hill shouldn’t be too steep: Your test shouldn’t be too fast, otherwise, you’re mostly measuring aerodynamics, and small changes in rider position will affect your results more than your tires.
Calibrating Our Tests
All tests are only as good as their research methodology. We’re lucky that BQ Team rider Mark Vande Kamp has a day job as a senior research expert at SAP, the global business software company. He has decades of experience with applied research and analysis, and he’s been involved in our testing since Day 1. He’s also one of the best riders you’ll ever meet. Combined, this experience enables him to design good tests.
Reproducibility is one key of all scientific tests: If the same test is performed twice, the result must be the same. Simply ‘testing’ four tires and reporting the results is meaningless. At the very least, one tire must be tested twice to show that the results are reproducible. Even in a laboratory setting, changes in temperature or in the measuring apparatus can affect the results. With real-road testing, demonstrating the reproducibility of the tests is even more important.

Above is an example from our most recent tests: We tested the same tires (Rene Herse Extralights) in two widths to find out whether wider tires are slower than narrow tires. We ran the bike with 44 mm-wide tires four times, then with 28 mm tires five times, then with 44s twice again. All test runs are within 0.51 seconds of each other. The averages are 15.47 seconds (44 mm) and 15.43 seconds (28 mm)—essentially the same.
The speed of the tests above is 27.6 km/h (17.1 mph). We ran this test at relatively high speed, because we wanted to account for the potentially higher wind resistance of the wider tires. (We run tests to determine differences between casings, etc., at lower speeds, so there is even less variability in the data.) Based on this – and many other tests showing the same – we can say with confidence that at most speeds, 44 mm tires don’t roll slower than 28s.
Statistical Analysis
Statistical analysis is a standard part of all scientific studies. It shows we’ve been successful in reducing the noise in our data. Basically, it calculates the likelihood that our results are due to real differences between the test setups (in our case, tires, pressures, etc.)— and not simply due to random noise. For example, it’s doesn’t come as a surprise that the difference between the 44 mm and 28 mm tires above (0.04 seconds or 0.3%) is not statistically significant. (We checked just in case…) But what if we find out that one tire is 1% slower than the other? Is that a real difference, or just ‘noise’ in the data. The statistical analysis will tell us. We always cringe when somebody reports that “x is 0.78% faster/slower than y” without a statistical analysis. That’s like flipping a coin ten times, getting heads 6 times and tails 4 times, and concluding that the coin is heavier on the side with the head…
If our results are statistically significant and replicable (meaning that you get the same results when you run the same test again), this also means that critics won’t be able to argue that our testing is flawed. Nobody can claim that it’s impossible to maintain the same position or that wind affected our results: The statistical analysis shows that these factors were controlled, and that we can reliably detect differences between tires. Statistical analysis may seem like a difficult hurdle for amateurs to overcome, but the processes are relatively standard, and you should be able to find somebody versed in them to do the analysis.
Assessing Tire Tests
Two things are essential to obtain meaningful results:
Tests must replicate the real world
If a tire test shows higher pressures rolling faster, that’s a big red flag. Higher pressures don’t roll faster – this has been shown many times and is now widely accepted. Even pros no longer run their tires at 8 bar (120 psi)… If test results don’t replicate the real world, something is wrong. (Usually, it’s that they don’t measure the suspension losses.)
Tests must be performed carefully
Running the same tire multiple times is essential, since it’s the only way to determine how reliable our data is. A statistical analysis is standard scientific practice – it allows figuring out which differences between measurements are real, and which are just ‘noise’ in the data. Reputable labs and good researchers all do this.
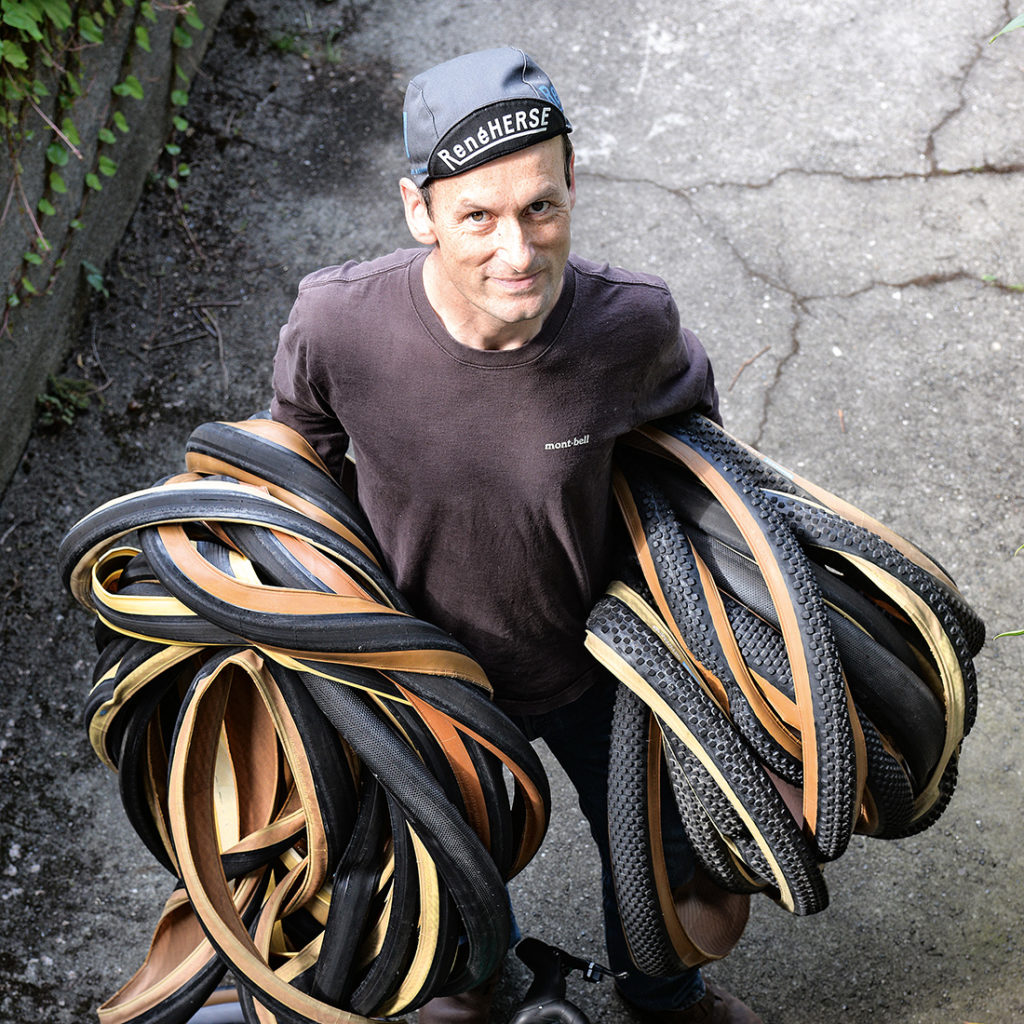
Conclusion
The challenge in conducting real-road tire tests lies not in the cost of the equipment: For the most meaningful tests, we need little more than a road with a constant slope, a bike, several wheelsets, and a stopwatch. The challenge is in setting up and conducting the test: Selecting a well-suited road – most don’t have a uniform gradient. Finding a day with constant conditions – we check the weather forecast, and we’re prepared to cancel our test session if even the slightest air movement springs up. And making sure the rider does not change positions during the test. All this requires time and skill, but not much money. It’s also the reason why real-road tests are difficult to perform for big companies with engineers whose working hours are limited and who need to produce results on a schedule. Real-road tire testing can be tedious (rolling down a hill hundreds of times in the same position) and frustrating (waiting for perfect conditions can take months).
Testing tires under real-world conditions is key to developing tires that perform better in the real world. Testing our casings, rubber compounds, and tread patterns under real-world conditions is one reason why Rene Herse tires perform so well. It’s also the reason why our tires are often different from those of other makers—each tire is optimized for the tests used in its development. A tire that’s optimized for a lab test is going to be different from a tire that’s optimized by testing in the real world, on real roads, with a real bike and real rider.
That also means that if ‘independent’ testers examine our tires on steel drums, the results will be disappointing—and misleading. Tires developed on steel drums test better on steel drums, but perform worse in the real world, and vice versa. Real-road tire testing is at the root of what makes Rene Herse tires different. It’s what makes them perform better where it matters: in the real world.
In the next post, we’ll look at some results of our latest tire tests…
Further reading:
• Our book ‘The All-Road Bike Revolution’ discusses the research that has revolutionized our understanding of how bikes work: tire performance, frame stiffness, frame geometry and every other aspect that determines the performance, comfort and reliability of your bike.
• This post was adapted from a more detailed article in Bicycle Quarterly 73 (Autumn 2020).
• The results of our latest tire tests.