Introducing Rene Herse Stems
They are here! What is probably the most iconic stem of all time, the Rene Herse stem, is now available again, updated for the 21st century. And we’re not just making the stem, but a complete, integrated system consisting of stem, decaleur and light switch, plus a few other parts.
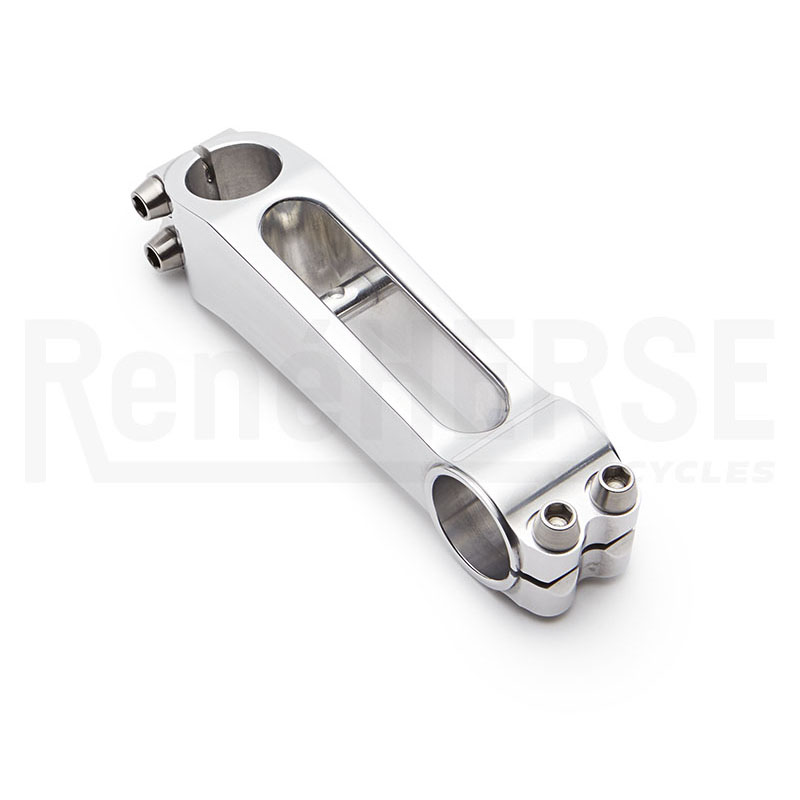
Typical of René Herse’s rational approach to bike components, the stem surrounds the steerer tube and the handlebars with just a minimum of material, and then connects them with two bars of aluminum. “A hole surrounded by a bit of aluminum,” is how Roger Baumann, one of the fastest riders on the Rene Herse Team, described it. As a result of this minimalist approach, the stem is superlight – just 160 g for the 90 mm version. And that includes the bolts and the flex-free cable hanger for centerpull or cantilever brakes. We’ve updated this iconic stem with titanium hardware that’s tightened with a 5 mm Allen wrench.
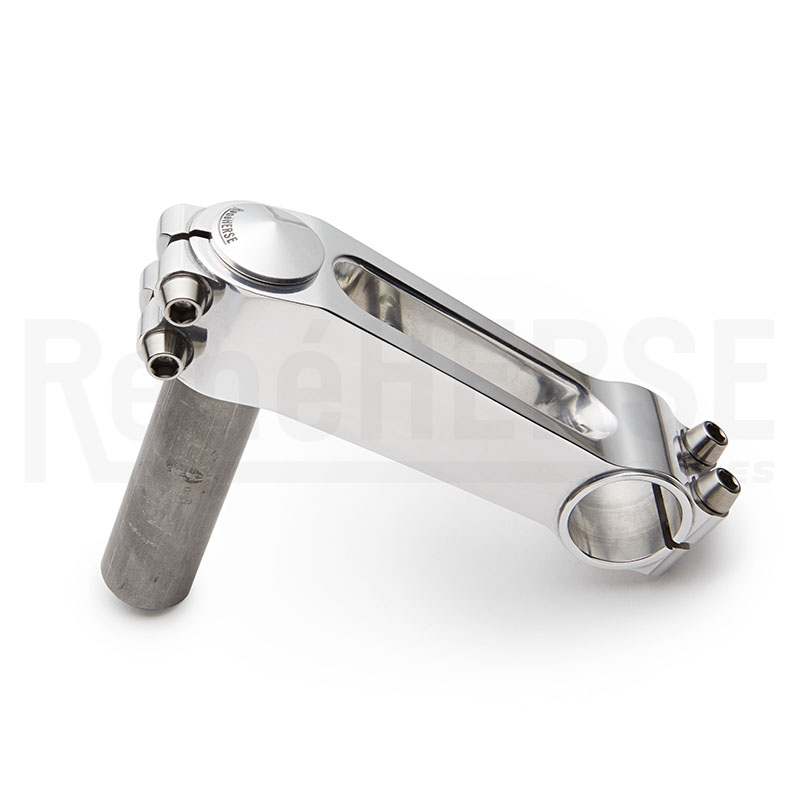
The stem’s attachment is unusual, but it makes a lot of sense: A tube is brazed into the standard (threaded) steerer of the fork, and the stem clamps to that tube. This allows the stem to be smaller (and lighter) than if it had to surround a larger 1″ or 1 1/8″ steerer. It also means that the inside of the steerer tube is empty, leaving room for a light switch (see below).
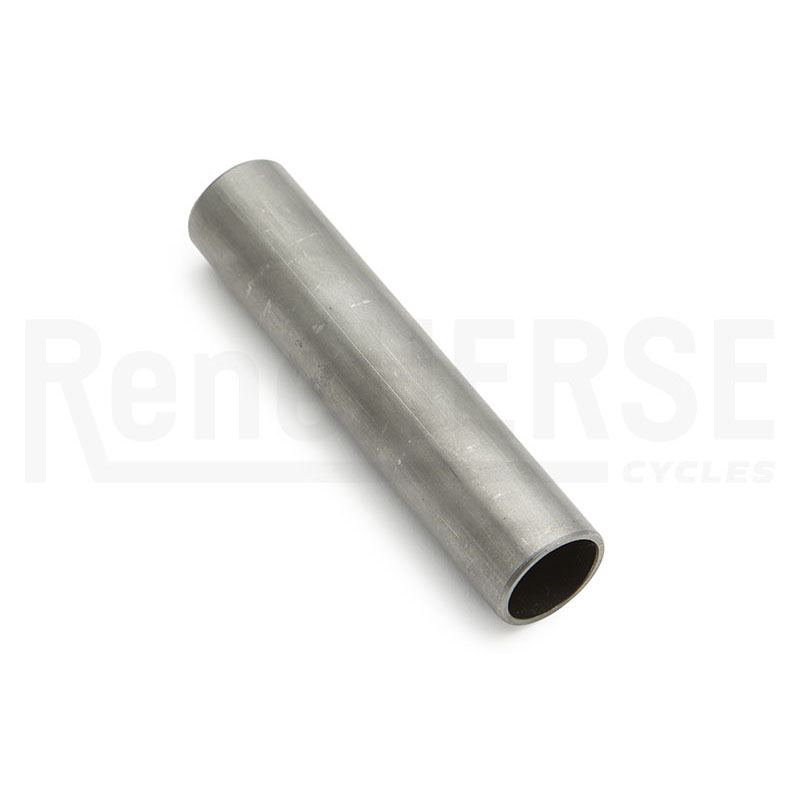
Of course, we also made the tube that you need to attach the stem. The tube is available with two wall thicknesses: 1.5 mm for most applications and 1.8 mm for heavier riders who like their bars high (which stresses the tube more).
The tube is an easy retrofit if you have a bike with a standard (threaded) 1″ steerer. You can either braze it into the steerer tube. (The steerer is usually not painted, so there’s no repaint needed.) Or you can glue it in with aircraft-grade epoxy. The surface area is large enough – make sure that both surfaces are clean to get a perfect bond. As always with frame modifications, consult with a qualified framebuilder.
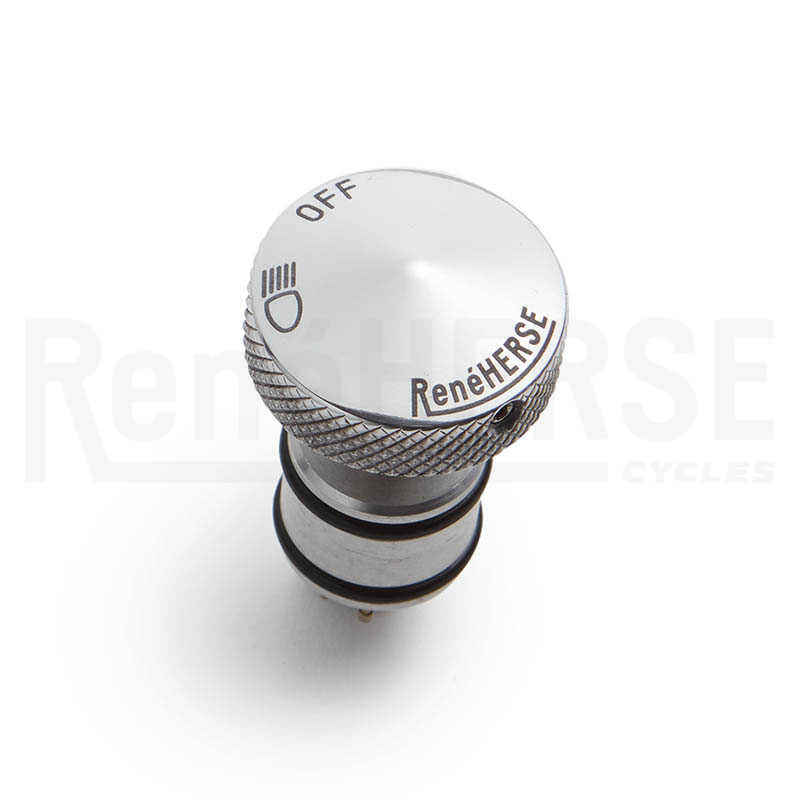
The Rene Herse Light Switch is a part I’m especially proud of. I developed it and made one for myself way back in 2007, because I was tired of fumbling with my lights, not just when it got dark, but also when I rode through tunnels in the mountains. In my car, I can turn on all the lights with a single switch that’s right next to the steering wheel. No need to stop, get out and turn each light on individually… I wrote about it in Bicycle Quarterly, and it’s inspired others to make their own. Now you can get one for your bike without needing to machine the parts…
The icons for the lights laser-engraved into the top cap, so you can look down and see whether your lights are on or not. (They are engraved rather than printed on, so they won’t wear off like the ones in my car…) The knurled surface is easy to operate even with gloves.
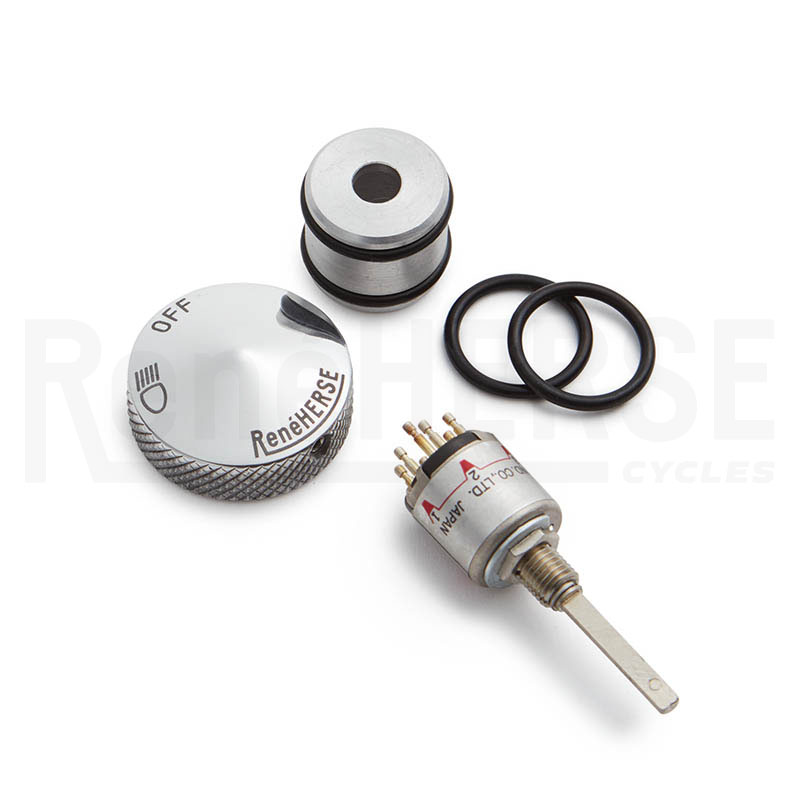
Inside is a top-quality switch that operates with beautiful precision. The entire unit is press-fit into the steerer tube, so it’s easy to remove when you disassemble the bike for Rinko. (You can also take off the top cap with a 1 mm Allen wrench.)
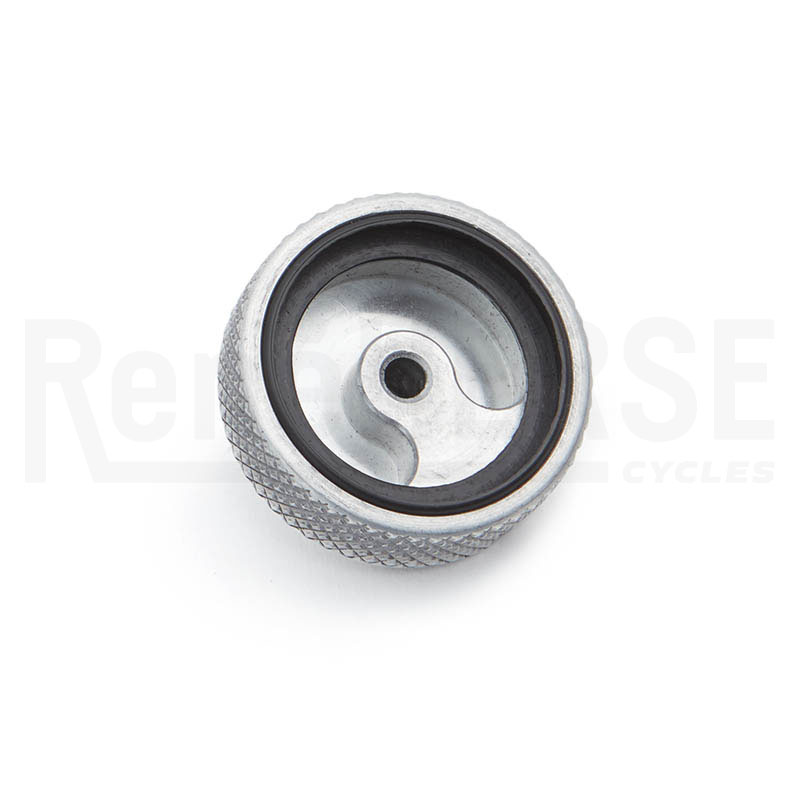
The top cap is hollowed out to save weight – the entire switch with all its parts weighs just 22 grams. A Delrin insert makes sure that the switch rotates smoothly on the stem tube. And since the cap drapes over the sides of the tube, there’s no risk of water getting in.
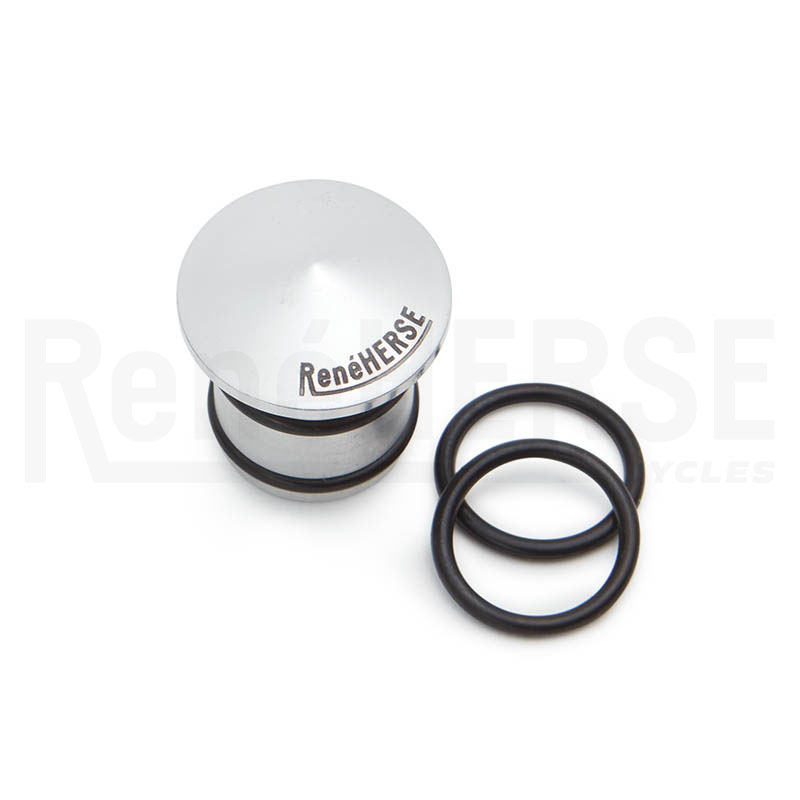
If you don’t run a light switch, there’s a simple top cap for the stem. Both the light switch and top cap come with two sets of O-rings for a perfect fit, no matter whether you run the stem tube with 1.5 or 1.8 mm walls.
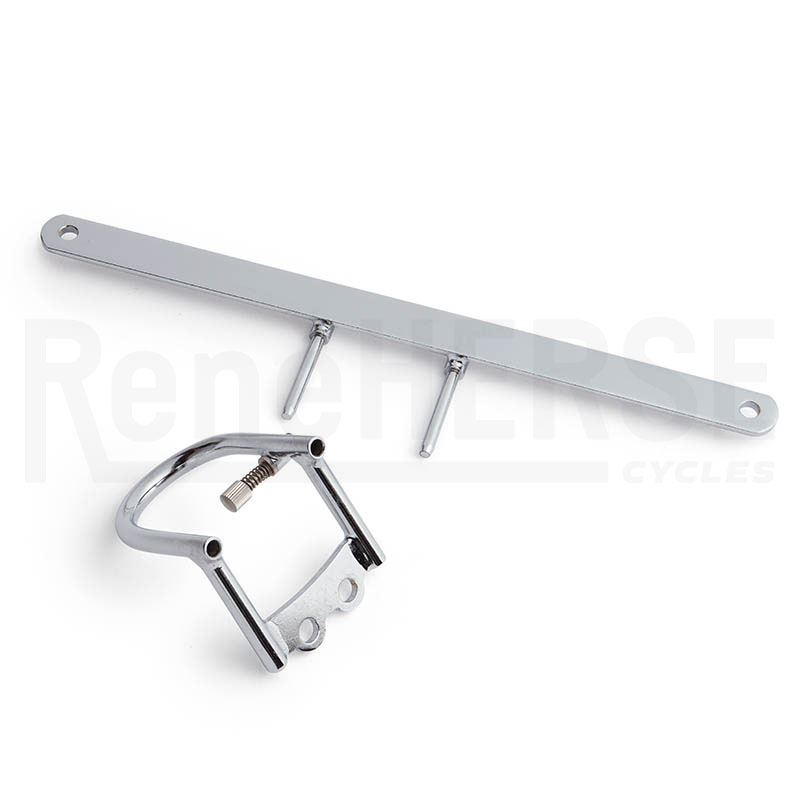
There’s also a special decaleur for the new Rene Herse Aluminum Stem. The plate that attaches to the stem is shaped to fit into the recesses for the stem bolts. Apart from that, the decaleur uses the same locking mechanism like the other Rene Herse decaleurs – licensed from our friend, the great (and much-missed) Japanese constructeur H. Hirose. The bag remains attached securely – even if you ride across rough terrain at high speeds. Yet when you want to remove the bag, you simply push the button and pull it upward.
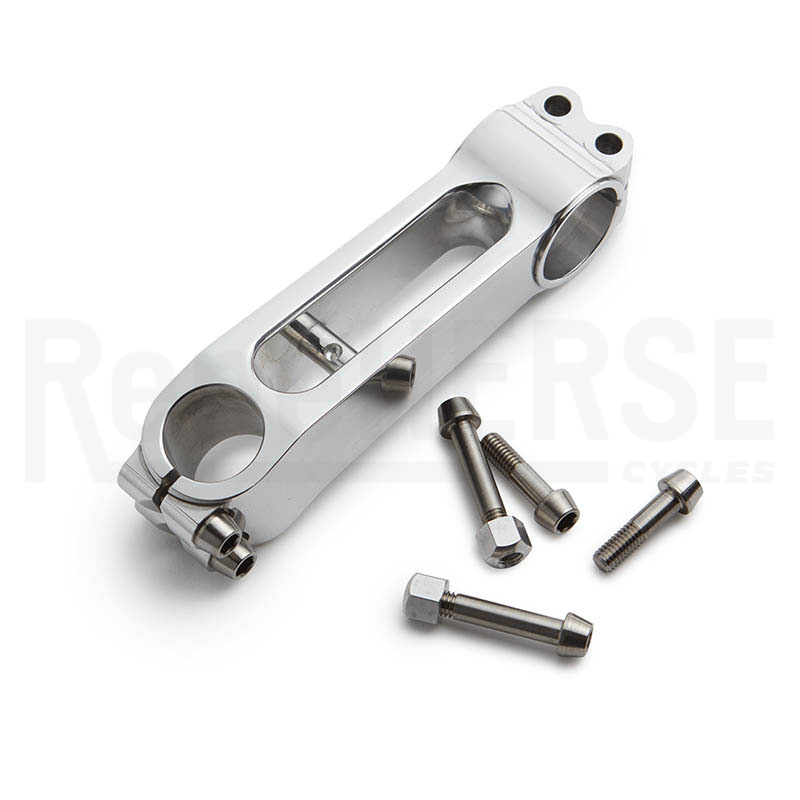
The new stems are available in four lengths: 60, 80, 90 and 100 mm. They come in two versions: The standard version has threaded holes for the steerer tube and the handlebar clamps. The version for a decaleur uses unthreaded holes for the handlebars. It comes with longer bolts and aluminum nuts to clamp the decaleur.
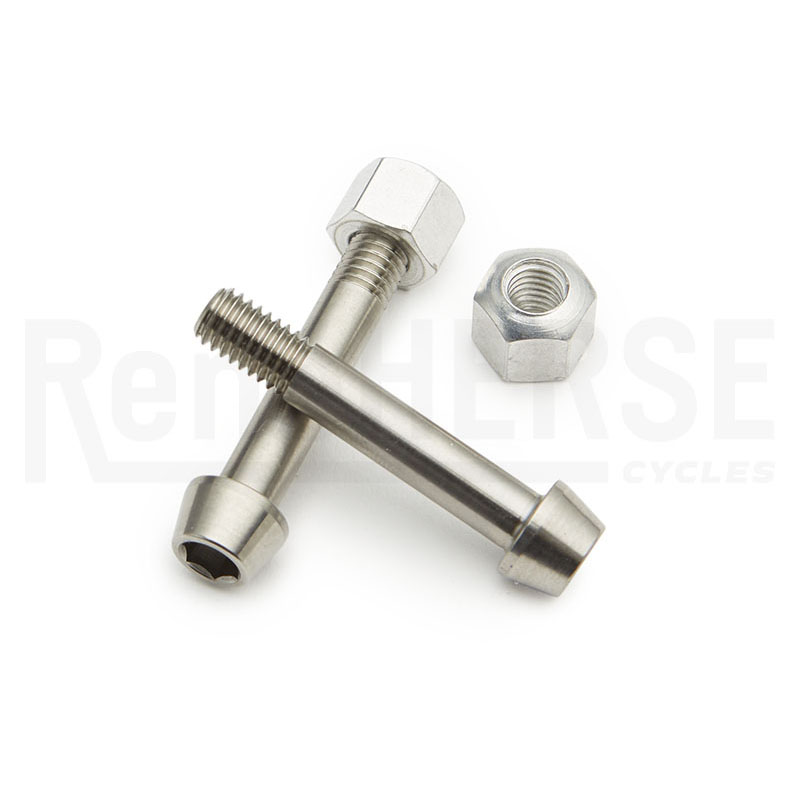
The stem bolts are based on Rene Herse’s iconic bolts with their triangular heads. We updated them with 5 mm Allen heads and made them from titanium. The bolts are large enough to take the bending loads if your handlebars aren’t exactly 25.4 mm in diameter. (This isn’t an issue with Rene Herse handlebars, but somebody may install other bars at some point in the future…) Thanks to their generous dimensions, the bolts are plenty strong. We made them from a high-strength titanium alloy, so they’re no heavier than the smaller steel bolts of most modern stems.
We also offer the bolts separately. That way, you can convert a standard stem for use with a decaleur. (Drill out the threads with a 6 mm drill.) They are also useful in other places. One attaches the headlight on my Oregon Outback bike, while another is used as a seatpost binder bolt.
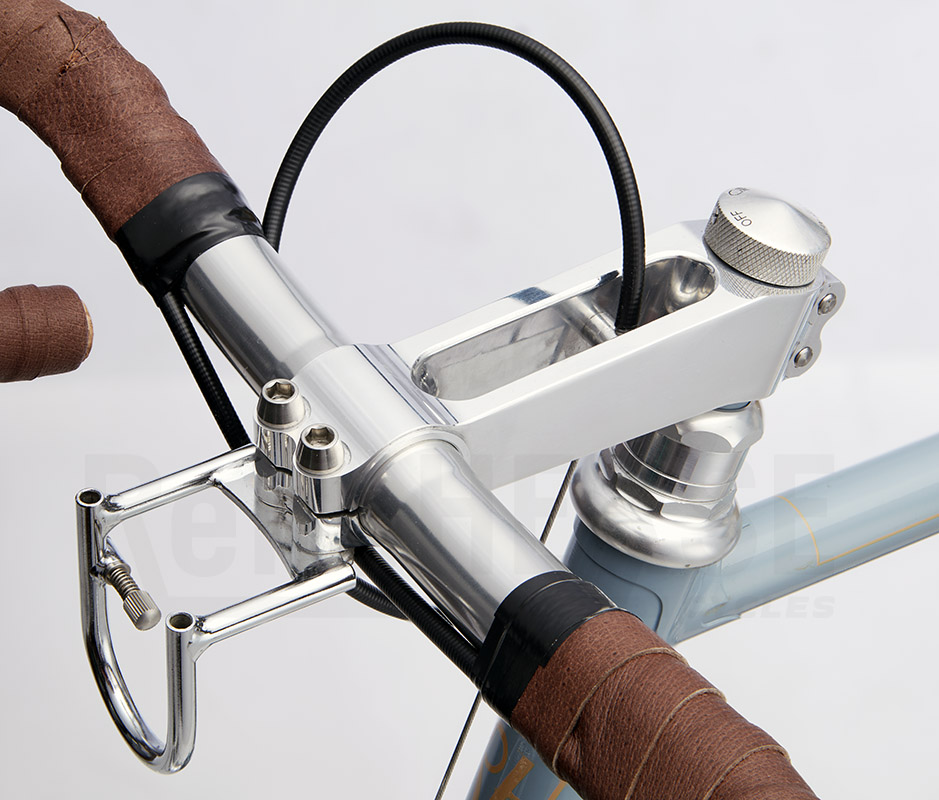
Despite the superlight design, the Herse stems are super-strong and not the least bit finicky when you set them up. There’s no risk of rotating the bars even on rough terrain, and you don’t need a torque wrench to tighten the bolts, either. The lip at the edge of the handlebar clamp distributes the stress, so you can run superlight bars without risking a failure.
We never introduce components without testing them extensively first. I’ve ridden one of the first production stems twice on the Oregon Outback (and many other rides) with zero problems. Of course, that doesn’t come as a surprise, since thousands of classic René Herse bikes with these stems were ridden on epic rides like Paris-Brest-Paris, the Raid Pyrénéen, the Concours de Machines and many other adventures with no reports of failures.
The stems are available in limited numbers right now. We aren’t sure whether we’ll be able to make more once these are gone – they are devilishly difficult to machine. If you get one, you’ll smile each time you look down at the hole. (But don’t take your eyes off the road too long!) It’s a fun part with excellent performance, and I’m glad we can share it with our customers.