Optimizing the Cantilever Brake
Cantilever brakes have traditionally been the way to make brakes for bikes with wide tires. Invented by Nicola Barra in 1936, they were among the first direct-mount brakes with pivots that attached to the fork blades and seatstays. This eliminated the flex that is inevitable with long brake calipers that reach all the way around the tire. Cantis greatly improved the braking, and the new brakes were popular on early randonneur and cyclotouring bikes. Decades later, they made their breakthrough into the mainstream with mountain bikes.
Cantis have many advantages. They are light – at 75 g, our Rene Herse cantis are among the lightest brakes in the world. The posts are standardized – you can mount almost any canti on almost any bike with canti braze-ons. They are reliable – there’s little to go wrong that a home mechanic can’t fix.
Despite all these advantages, you’ll be hard-pressed to find a new bike equipped with cantis. For mountain bikes, front suspension meant that there was no logical place to anchor the brake cable any longer, and it made sense to use hydraulic discs. As a plus, they had more braking power and required less hand force than most cantis.
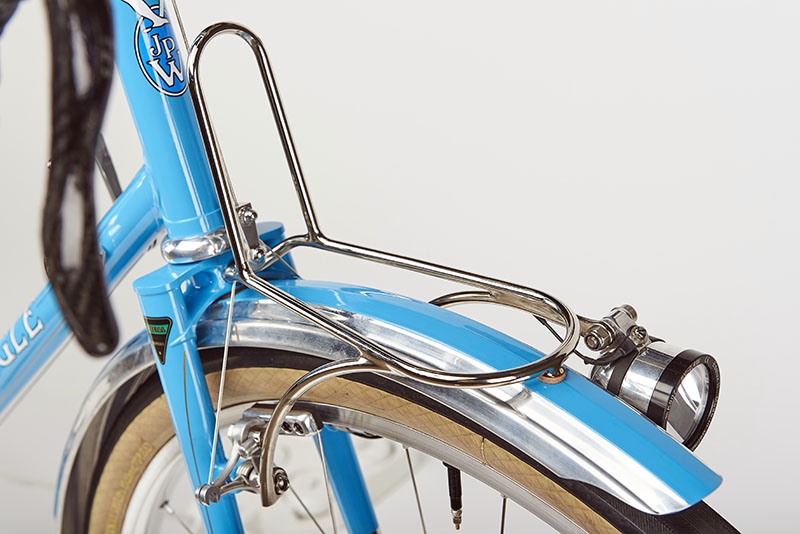
For road and all-road bikes, centerpulls eliminate the one inherent weak spot of cantis: Canti pivots are located in relatively poorly supported parts of the fork blades and seatstays, which can twist under hard braking. This means that the angle of the brake pad changes, resulting in non-linear braking.
That is the theory. I wasn’t a big fan of cantis… until we started to work with Peter Weigle on a bike for the Concours de Machines, the competition for the lightest fully equipped all-road bike. Our goal was to build a no-compromise bike: reliable and fully equipped with fenders, generator lights, rack and wide tires. Yet our target weight was no more than 20 pounds (9.1 kg) – fully equipped, including the bell and pump. Peter was going to pull out all the stops with a featherweight frame and many modified components. Every gram counted – discs were out of the question, and even centerpulls didn’t look like the best option. I was willing to make some compromises in brake performance to reach our target weight.
So we began to look at cantis.
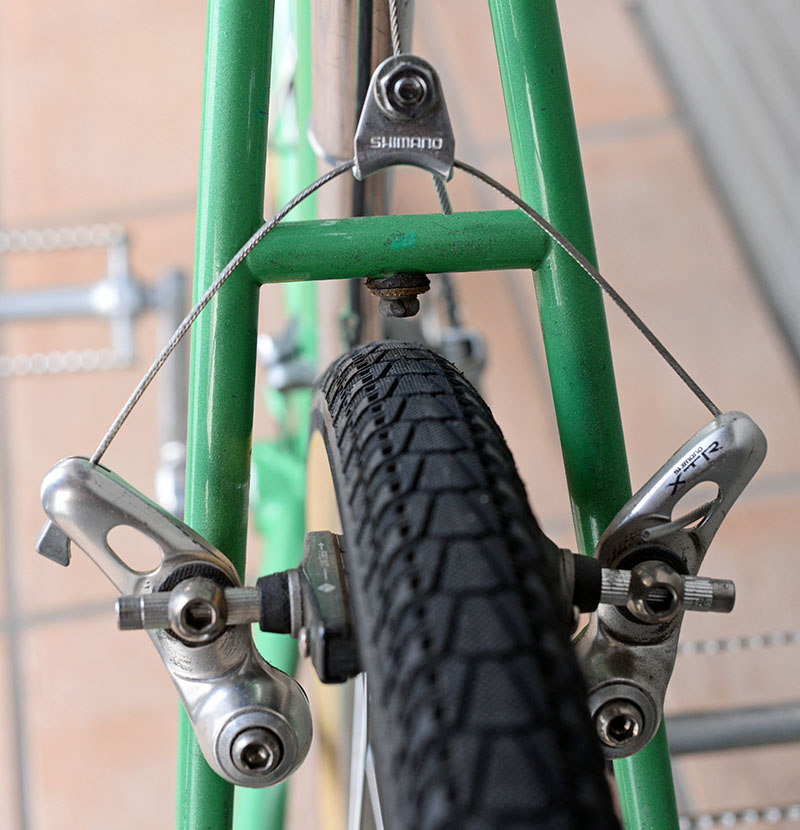
As we thought about how to optimize cantilever brakes, we realized that most cantis are – how to put it politely? – suboptimal in their design. Take the straddle cable: It’s made from the same thick wire as a brake cable, which makes it too stiff to conform to the straddle cable yoke. (You can pre-bend it, but it’s never perfect.) When you brake, the first part of the lever travel only pulls the straddle cable taut, before can you apply braking force to the pads.
We calculated the stresses on the straddle cable and realized that a thinner cable would be strong enough. The only problem is that the cable is clamped to one brake arm. Every time you brake, the cable’s exit angle changes, and the cable flexes acutely where it leaves the clamp. Flexing weakens the cable until individual strands start to break, and the cable frays. The thick straddle cable is needed to prevent premature failure.
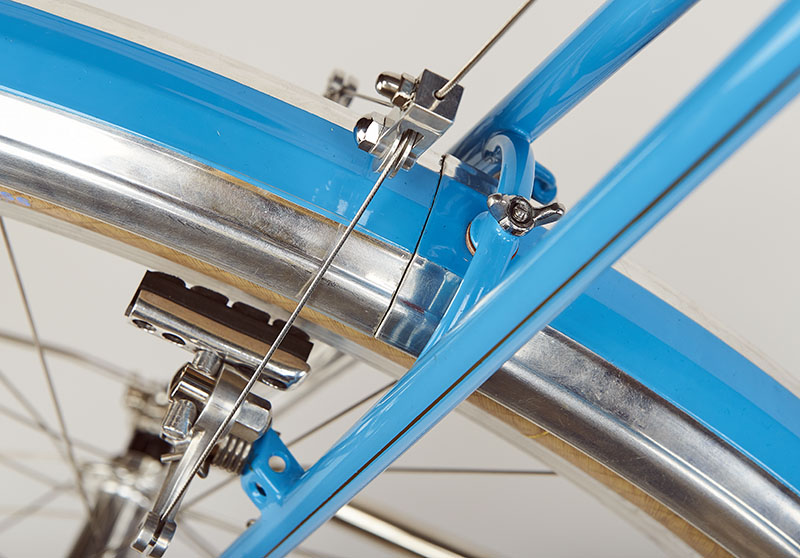
What if we allow both ends of the straddle cable to swivel in the brake arms? Now we can use a thinner straddle cable, which wraps tightly around the cable hanger. There’s no lost motion, and we no longer lose a third of the brake lever travel to flex before the brake finally begins to squeeze the pads. Which means more braking power – plus we can set the brake pads further from the rim without worrying about the brake lever bottoming out against the handlebars.
Another issue of most cantis is the fiddly adjustment of the brake pads. You want the pads to have a little toe-in (the front of the pads should touch the rim first). Most systems to adjust the pads are hit-or-miss, because the pad angle inevitably changes as you tighten the bolts.
When you think about it, the toe-in only needs to be set once. The angle of the brake pads is determined by how the brake posts are brazed onto the frame. (There are always minor tolerances.) Rene Herse used his brakes only on bikes he built, so he simply bent the brake arm until he got the perfect toe-in. Once this was done, the customer never had to think about it again.
We realized that this was the way to go. Getting rid of all those spherical washers eliminates a lot of flex (and weight). And when it’s time to replace the pads, you don’t have to set the toe-in again, as the adjustment remains the same. (For riders who aren’t comfortable bending their brake arms, we offer a version with an angled washer that allows angling the brake pads without bending the brake arm.)
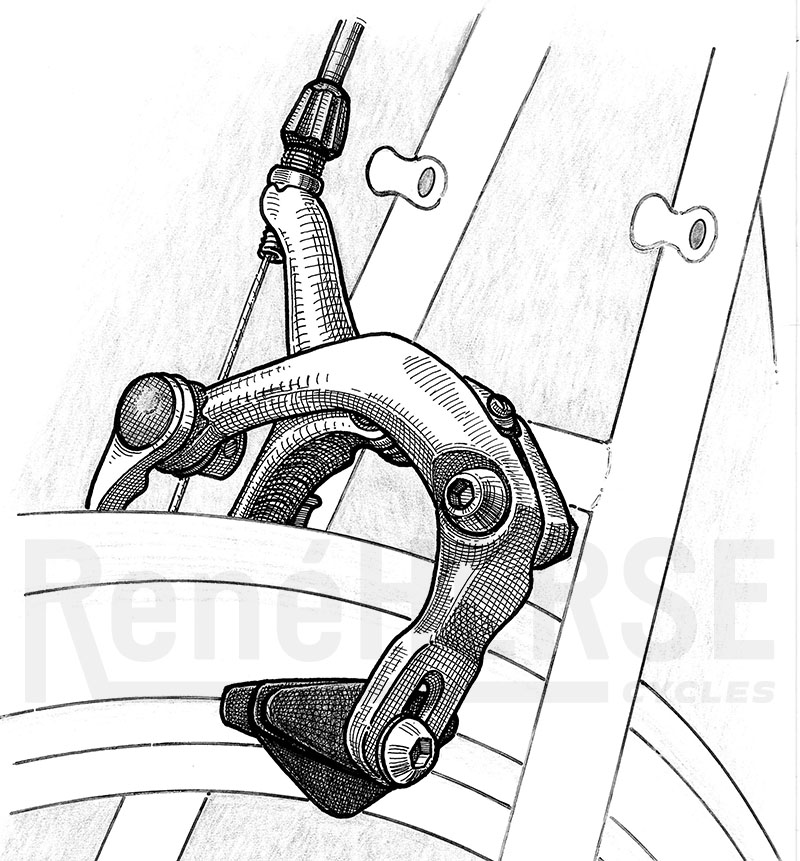
Another issue are the brake pads themselves: Many modern cantis use the same pads as sidepull brakes – they bolt right onto the brake arm. That means you don’t need special hardware (which is expensive to make), but there is a big disadvantage when the time comes to adjust for pad wear. With canti brakes, you don’t want to use barrel adjusters: As the pad wears, it hits the rim lower and lower, until it can dive under the rim as you brake hard. Then you lose all brake power. (On sidepull brakes, the pads moves the opposite way and can cut into the tire, but the long arms reduce this effect.)
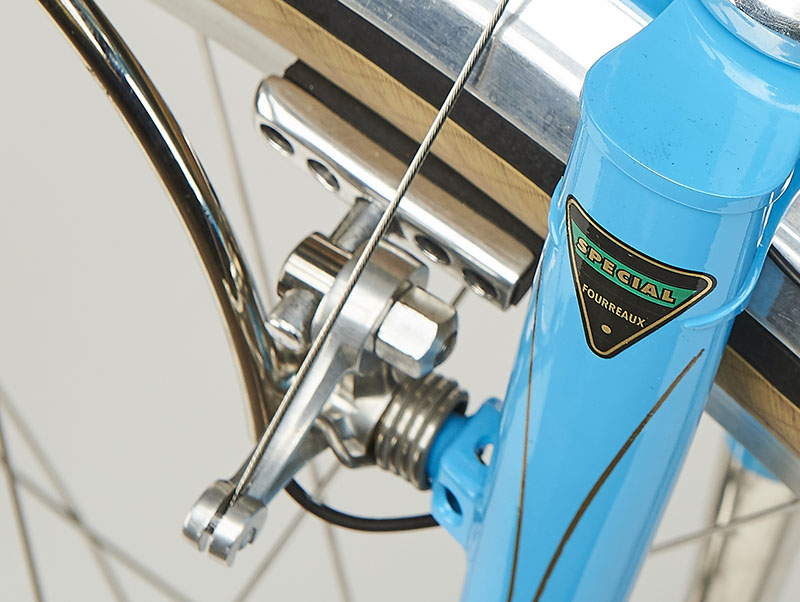
You need to adjust the angle of the pad as it gets thinner, which means fiddling with the toe-in adjustment again… unless you have proper canti pads with posts. Then you simply open the nut and slide the entire pad closer to the rim. Tighten the nut again, and you’re done.
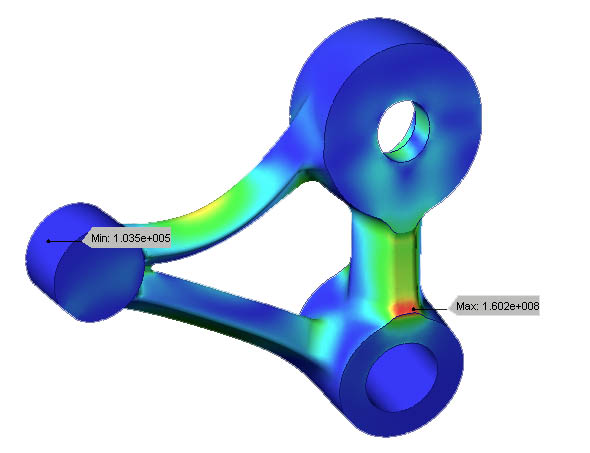
As for the brake arms themselves, you don’t want them to flex. When you pull on the brake lever, the entire force should be transmitted to the brake pads, with no power lost to flexing the arms. To achieve this, we optimized the shape using Finite Element Analysis (FEA) – a computer model that calculates the stresses. Blue and green indicates low stresses that will not cause significant flex. (The red dot is something known as an ‘edge error’ in the model, not a place where the stress is high.) The FEA also allowed us to pare the brake arms down to an absolute minimum, which is why they are so light.
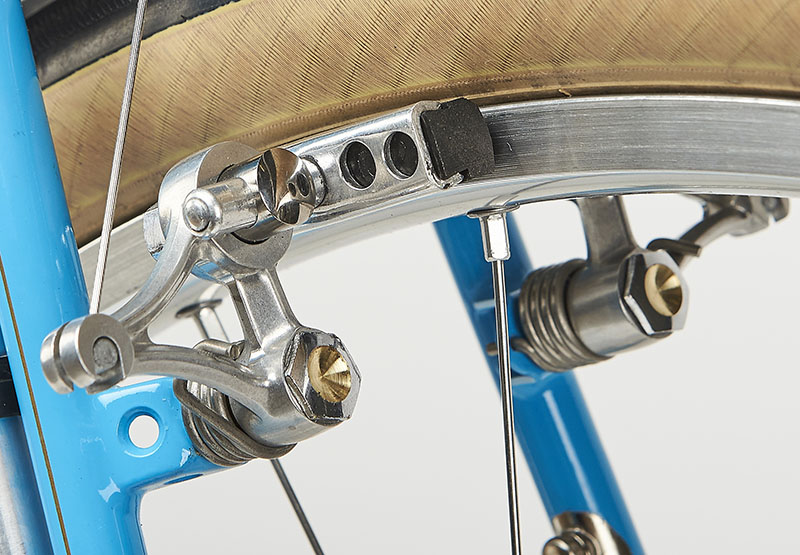
Minimalist brake arms must be forged to align the grain of the aluminum with the stresses. This makes the brake arms much stronger than carving them out of a big block of aluminum with a CNC machine. (There’s also less waste with forging, so it’s better for the environment.) The down side: Forging requires very expensive tooling. To us, it was worth the effort.
While we were stripping weight off the brake arms, we thought about the adjustment for the spring tension that most cantis have. You only need to adjust the tension if the two springs are not equal. If we can make springs that have equal tension to begin with, we don’t need the tension adjustment. That saves weight and makes the setup of the brakes even easier. In fact, our springs wrap around the brake arm, since there is no room for a hole.
We also thought about the hardware. Usually, replacing steel bolts with titanium isn’t a good idea, since the bolts are dimensioned for the loads that they experience. The eyebolts that hold the brake pads are an exception – they have to be big so the brake pad fits through them. Making them out of titanium saves weight with no loss of strength. (We offer less expensive steel bolts for riders who aren’t concerned about a few grams of weight.)
In this way, we analyzed, calculated and rethought every part of the brake. And then we made each part from the best materials and to the highest precision.
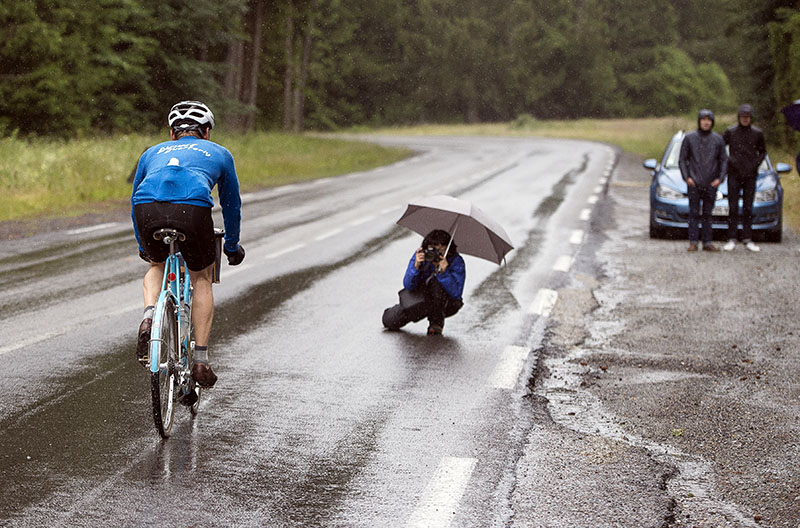
Did all this effort make a difference? The first test came during the Concours in France. The final stage included a long mountain descent in pouring rain, with numerous hairpin turns. I was surprised how well the Weigle braked. The cantis were so powerful that they scraped the water off the rims within just a few revolutions of the wheel, and the braking action was powerful, linear and easy to modulate.
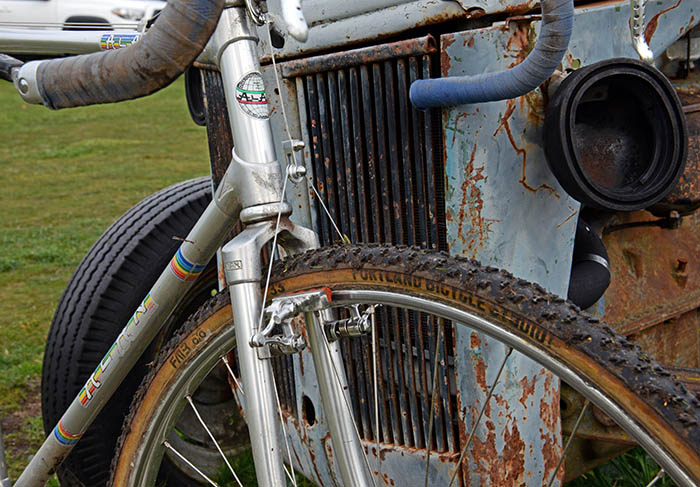
Before we release our products, we test them extensively, and so I mounted a set of the prototype cantis on my cyclocross bike. My Alan always had suffered from pronounced fork judder at low speeds – not really a problem when racing (where you brake only at high speeds), but annoying nonetheless. I thought this was due to the stiff fork and flexible steerer, but to my surprise, the judder was gone with the new brakes. It appears that the flex and play in the pivots of the old cantis was the main culprit.
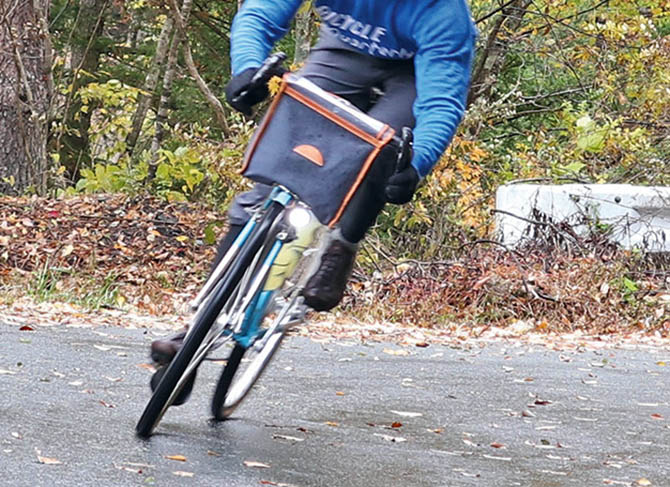
Since then, I’ve ridden many miles with our Rene Herse cantis, often in challenging conditions. I’ve realized that 97% of the issues I had experienced with other cantis were due to their design and manufacture, and only 3% were caused by the pivot location that is inherent in all cantilever brakes.
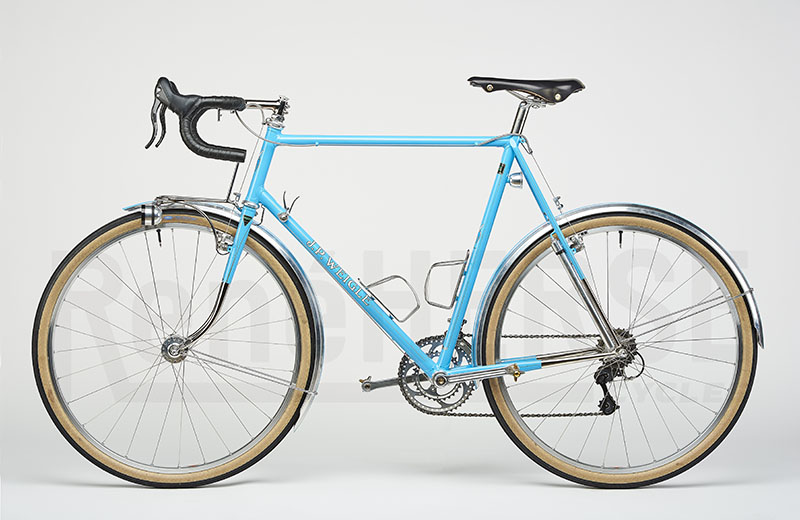
Further reading:
• More about the J. P. Weigle from the Concours de Machines.
• The full report from the Concours, plus Peter Weigle’s story of how he built this amazing bike, was published in Bicycle Quarterly 61.