Why Rene Herse tires score best in real-road tests
An acquaintance once remarked: “Isn’t it funny that Rene Herse tires always score best in your tests?” There was a twinkle in their eye, and their voice made clear that this was a gentle ribbing and not an accusation, but it got me thinking… It’s easy to suspect foul play when we test our own products. The reality is a bit different: The reason our tires perform best in our tests is because that’s what we design them to do.
Serious tire makers test prototypes of their high-end models to optimize performance. It’s part of R&D. However, there are different ways of testing tires. Our tires are optimized with the help of our real-road testing, so it’s natural that they perform well there. If we used another maker’s tests, I wouldn’t be surprised if their tires came out ahead of ours.
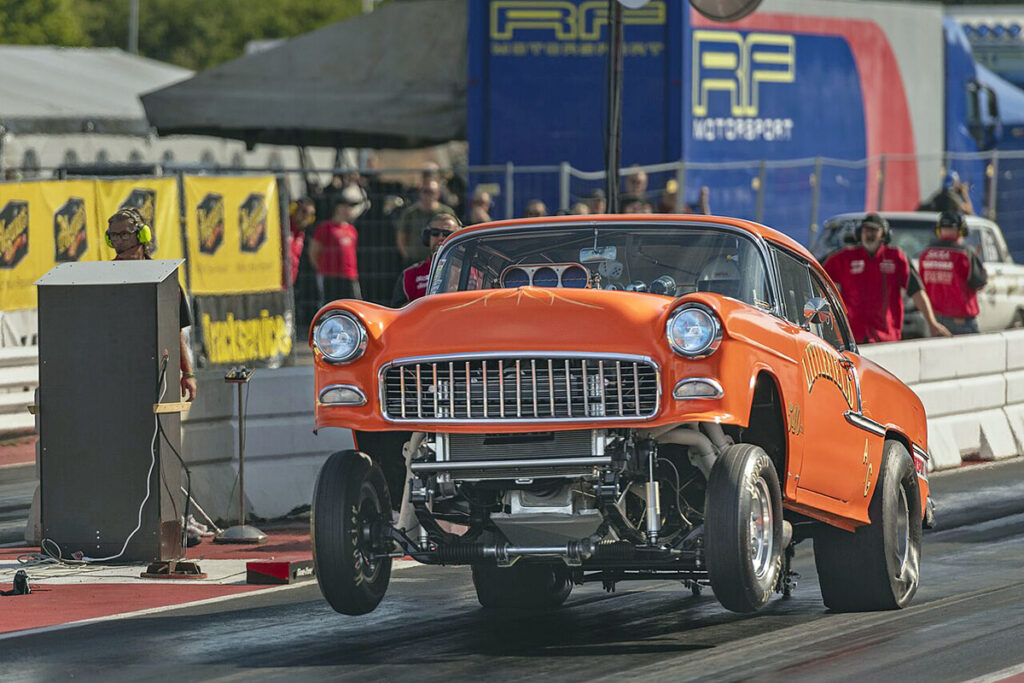
To understand what I mean, let’s digress into car design for a moment. Imagine you want to develop the fastest car.
If you use a drag strip for testing, your car will have huge horsepower and ultra-wide rear tires. The front tires aren’t really important: How well your car corners doesn’t matter for your test.
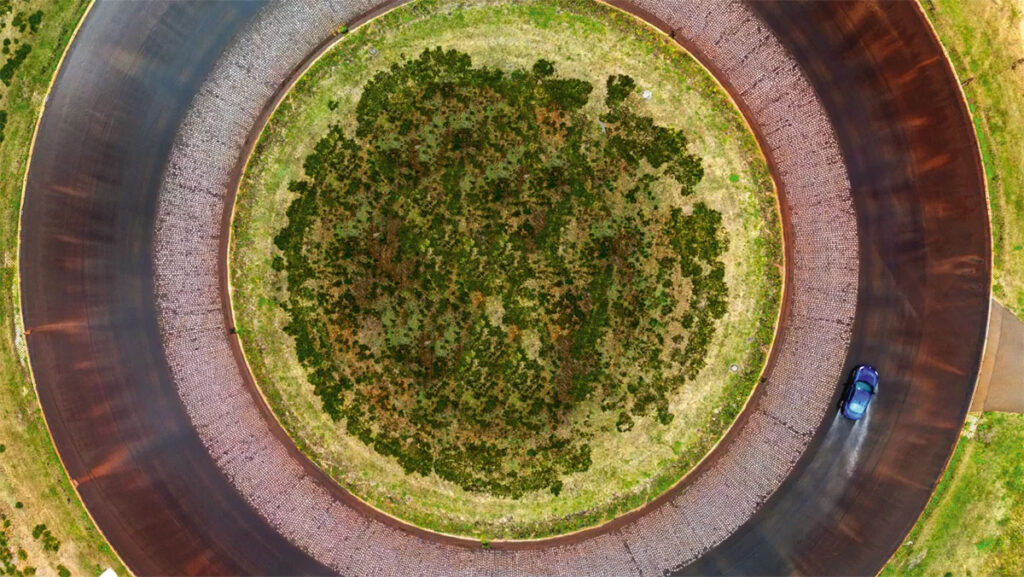
If you care about driving on mountain roads, you want a car that handles well. To quantify how a car corners, you could use a skidpad—a road that forms a perfect circle, so you can measure how fast your car can go before it loses traction. The magazine Road & Track sometimes tests cars that way. It’s objective, because you can measure the g forces. But it doesn’t factor in how the car transitions from straights to curves, how it handles changes in road camber, and how abruptly it breaks away when it reaches the limit. Those are important factors that you can’t measure on a skidpad. A skidpad favors wide tires and an ultra-stiff suspension that keeps those tires parallel to the surface, but little else.
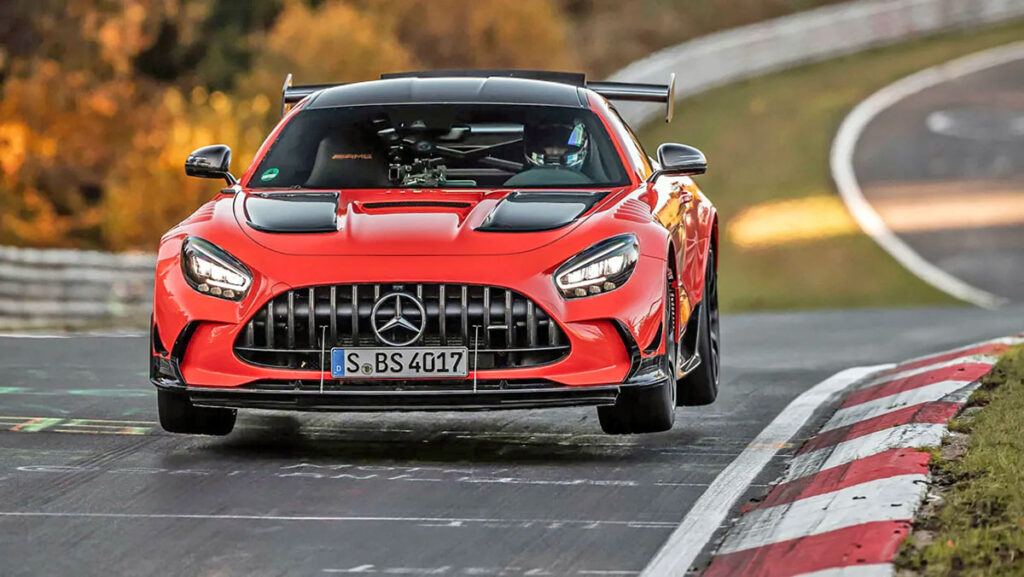
Searching for a better test, many car manufacturers now go to the Nürburgring, an old racetrack in Germany that winds through the Eifel Mountains. A fast lap time around that 13-mile circuit has become major bragging rights. For this test, you need a sophisticated suspension and, ideally, light weight, in addition to horsepower and grippy tires.
It’s easy to see that your ‘fastest’ cars will look quite different, depending on which test you use to develop it. A car designed for the drag strip will ace the straight-line test, but it’ll be useless on the skidpad with its constant lateral g-forces. And a car designed on a skidpad will perform sub-par on the Nürburgring, where conditions are constantly changing.
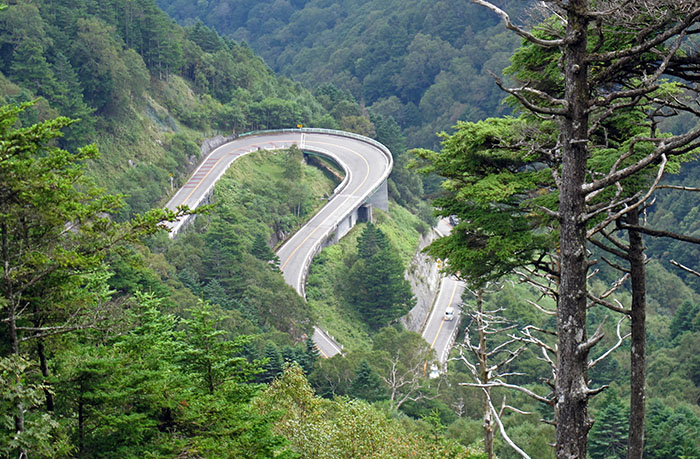
What it comes down to is this: Which test is most relevant to us? With cars, the Nürburgring is more relevant for real-world performance than a drag strip or a skid pad.
With bicycle tires, the situation is similar. Different tires will perform best in different tests, and it’s up to us to decide which test is most relevant to our riding.
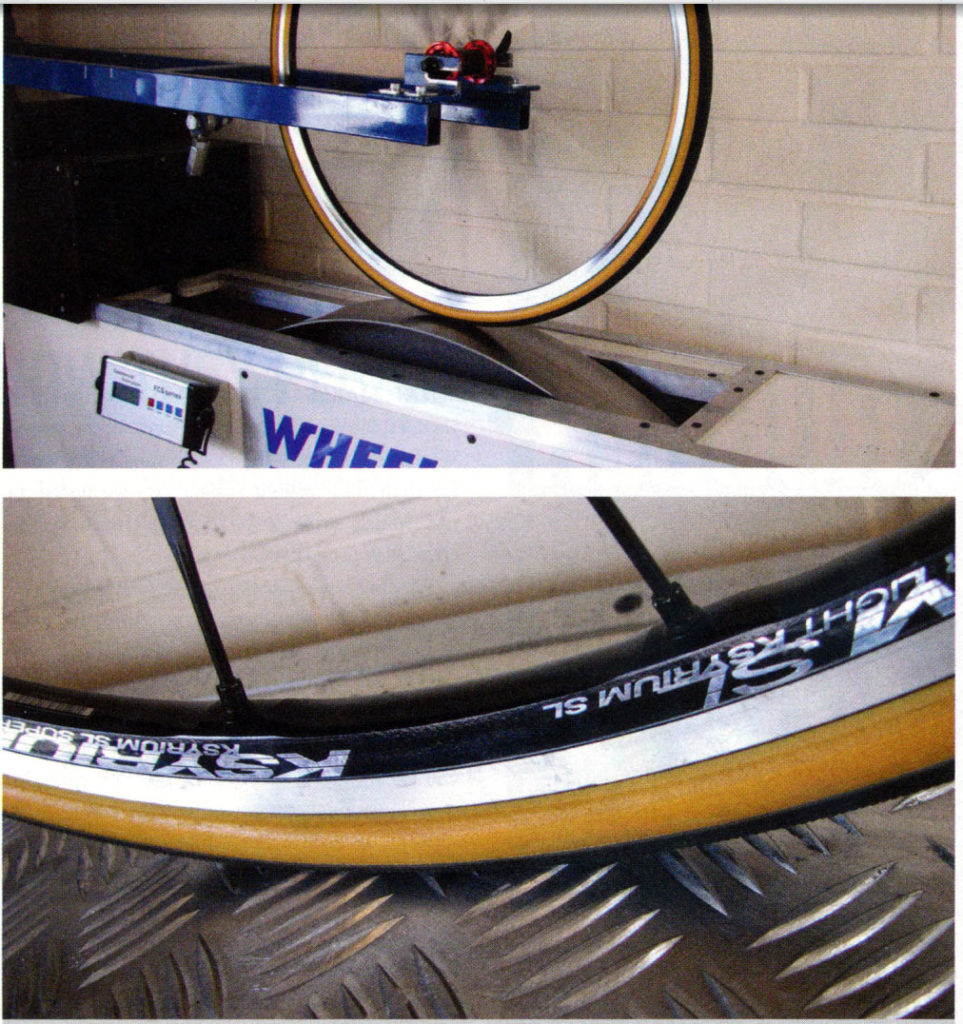
Most tire manufacturers use steel drums to test their tires. Here is how this works: You measure how much power you need to spin the drum without a wheel. Then you add a wheel and tire, and you measure the power it takes to spin the drum again. The difference is the rolling resistance. Testing on steel drums is pretty much the industry standard. It’s very accurate, as long as you keep the temperature in the testing room constant. And once you have the machine, you can test anytime you want with relatively little effort. Some makers use a patterned drum to simulate rough roads. Even then, the drum is only testing tire and wheel, but not the complete system of bicycle and rider.
It’s no secret how you optimize a tire for drum tests:
- First you minimize how much energy it takes to flex the tire. You’ll choose a thin casing, because this absorbs less energy as it flexes where the tire touches the drum.
- Second, you also minimize how much the tire flexes altogether. Less flex means less energy lost. So you’ll make your casing stiff to minimize that flex. And you’ll spec a hard tread rubber, again to minimize flex.
In other words, you want a hard tire with a thin casing to ace the drum test. (That’s also why high pressure scores well on the drum—it makes the tire harder.)
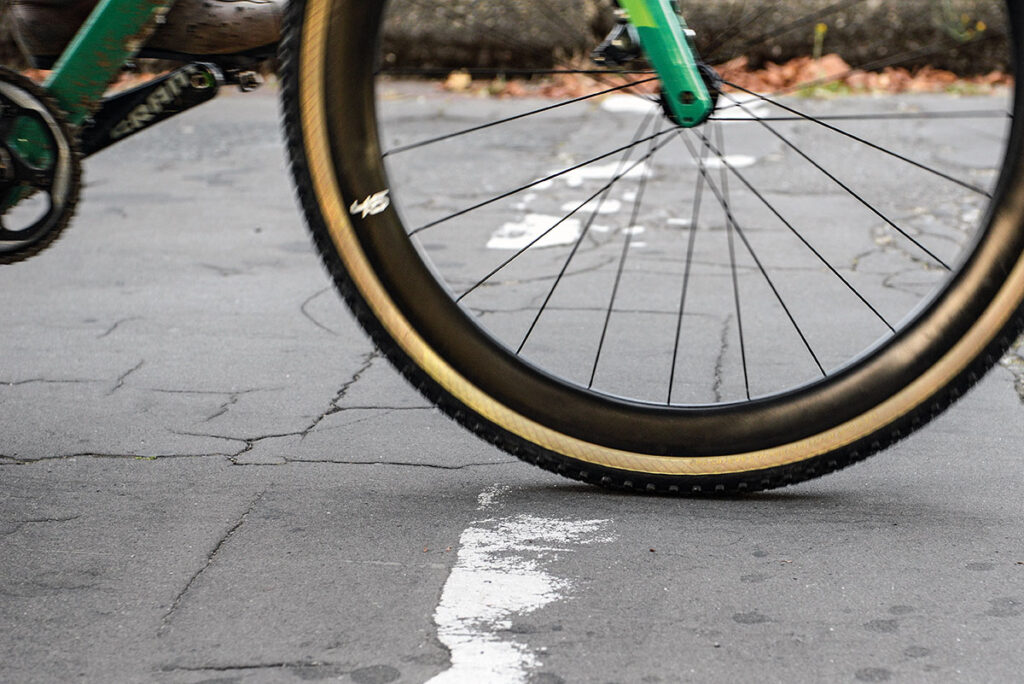
If you test on real roads, there are important differences. To start, you want to minimize the energy lost to flex, just like on the drum. So you want a thin casing, too. That is why supple tires score better on drums than tires with thick casings. In fact, the Rene Herse Snoqualmie Pass 700C x 44 is the fastest wide tire ever tested by www.bicyclerollingresistance.com. But that’s not the whole story, and if we optimize our tires for drum tests in the lab, we will actually make them slower on real roads.
To make a tire fast on real roads, you need to minimize vibrations. When the bike vibrates, the rider’s body tissues rub against each other. This causes friction, and it slows down the bike. The technical term for this is ‘suspension losses,’ and it was discovered by the U.S. Army in a study of tank seats half a century ago. Our research has shown that suspension losses are also an important factor in bicycle performance.
In the drum test, you don’t pick up suspension losses, because there is no rider. On real roads, suspension losses are very significant. On rough surfaces, these losses can amount to more than 100 watts. On rumble strips—the corrugations found on the side of highways to wake up sleepy drivers drifting off the road—we’ve measured as much as 290 watts lost to vibrations. That’s almost a worst-case example, and it shows how much energy you can lose if your bike vibrations. At the other end of the spectrum, suspension losses are significant even on smooth roads. To make your tires fast, you want to minimize vibrations as much as you can. (That’s why high pressures don’t offer an advantage on real roads—they increase the vibrations just as much as they reduce the flexing of the tire.)
So you’ll need a thin casing, but—unlike for the steel drum—it should not be stiff. The casing needs to be supple, so it’s easy to flex. That way, vibrations are not transmitted to bike and rider, but absorbed in the tire casing with a minimum of energy loss. Another big difference is in the tread rubber. Hard rubber rolls faster on steel drums, but soft rubber actually rolls faster on real roads, because it conforms to the surface and transmits fewer vibrations. (Skateboarders have known this for a long time—boards with soft wheels roll faster.)
You can see how the ‘best’ tires are subtly different, depending on how you test them:
- Drum test: Thin, hard casing; hard tread rubber
- Real-road: Thin, supple casing; soft tread rubber
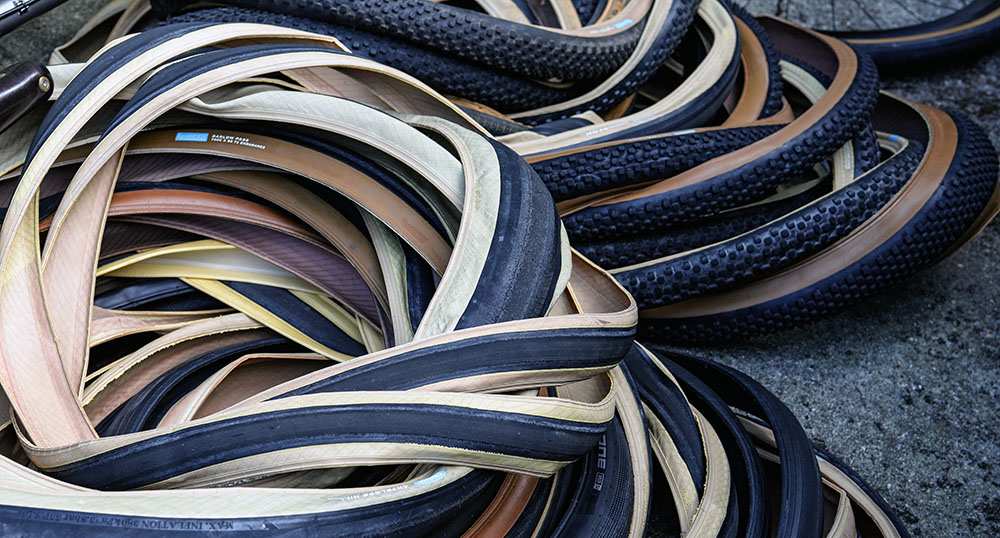
To show you how this plays out in the real world, let’s look at an innovation that made headlines a few years ago: tread rubber with long-chain polymers. Most famous is the ‘Black Chili’ compound from a big tire maker, but others use similar formulas. (As I explained last week, there isn’t much proprietary in tire materials.)
When our suppliers told us about a new rubber that would make our tires faster, we were excited. They had tested the new compound on their steel drums, and it resulted in significantly lower rolling resistance. We got some prototypes, using our tire molds and our casing, but the new rubber compound with long-chain polymers. We compared these prototypes to a set of tires from our normal stock. We tested these tires in our real-road roll-down tests.
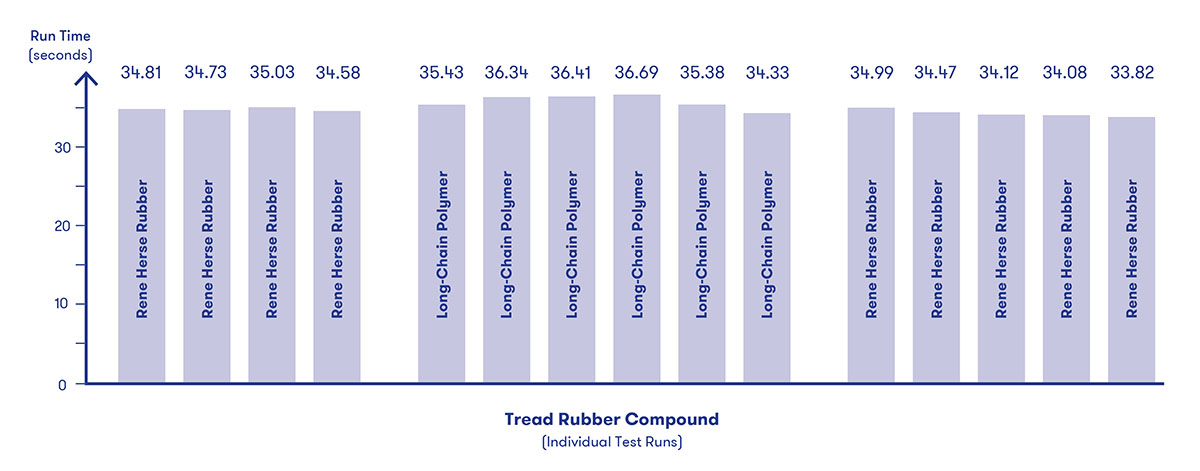
We did four runs with our existing tires, then six runs with the new tread rubber, then five runs with the existing tires again. Why do we test the first set of tires again at the end of our testing? Repeat testing confirms that conditions haven’t changed while we are testing. Even though we only test on days with zero wind and constant temperature, it’s important to double-check that we’re really measuring differences between tires and not changing conditions. For example, if the rider gets tired and changes position slightly, that might affect the aerodynamics. Or if a wheel bearing starts to act up, that might slow the bike. If nothing has changed, we expect the results from the first and last set of runs with the same tires to be the same. (They were in this case.)
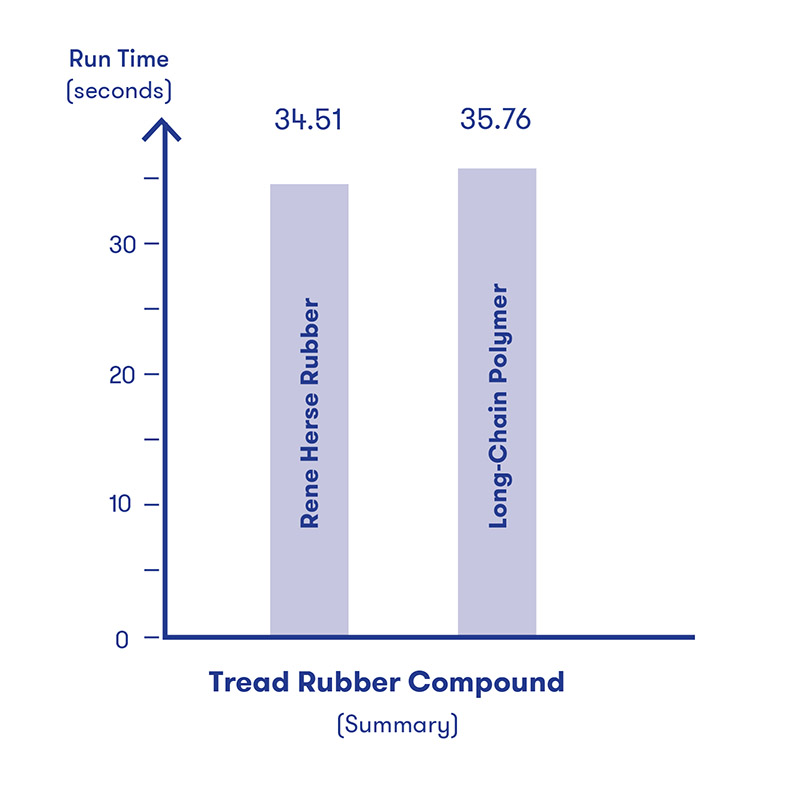
We expected the new rubber to roll faster—but we were disappointed: The long-chain polymer tread rolled significantly slower than our existing rubber compound. The graph above shows the average roll-down times for each tread rubber. We did a statistical analysis to make sure we’re seeing real results and not just noise in the data. The statistics confirmed that the new tread rubber with the long-chain polymers is slower.
Translated into power, the long-chain polymer rubber will cost you about 3 watts. It’s a small penalty—enough to notice if you’re riding with a well-matched group—but that’s just one of many factors that influence how fast a tire rolls. What is important here is that the ‘improvement’ (based on steel drum tests) actually made the tires roll slower on real roads.
Needless to say, we kept our existing tread rubber, because it rolled faster in our test. Other tire makers switched to the long-chain polymer rubber, because it scored better in their tests. Now you won’t be surprised if you see other tire brands rolling slower in our test. And if we’d use their test, their tires might be faster than ours. No surprise there—that’s what you’d expect.
So there’s nothing nefarious if each company’s tires perform best in their own tests. That’s how these tires were developed, after all. You could call it ‘designing to the test’—in the best way. We each design our tires so they perform best in our tests.
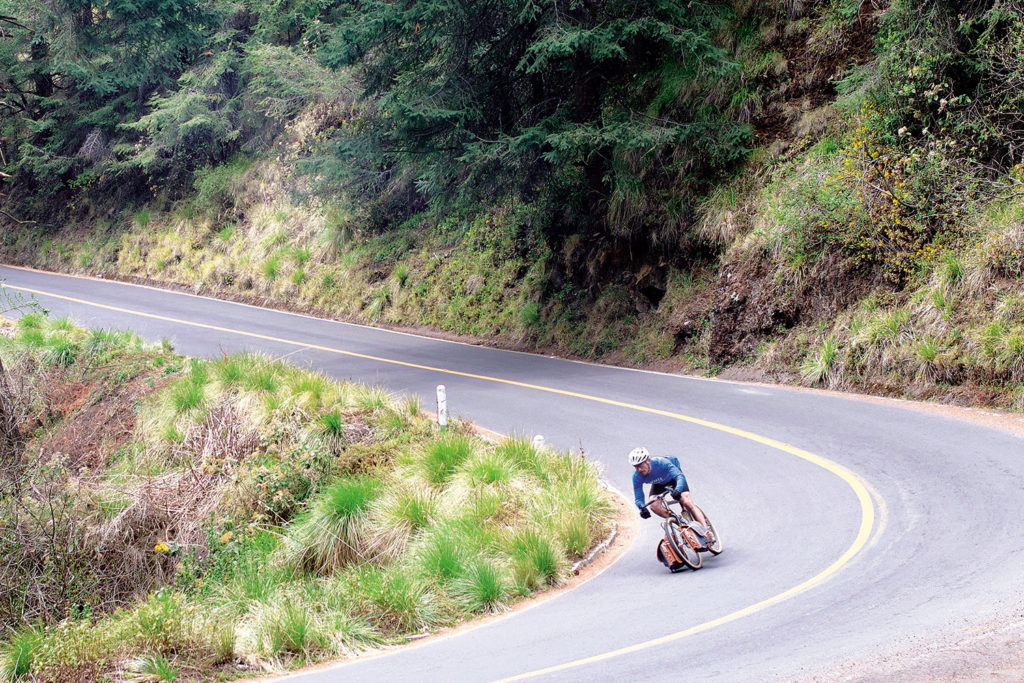
Riders now have to decide which test is most representative of the riding they do. If we return to the car analogy for a moment, do you want a car designed for a 1/4-mile straight-line sprint? Or one designed for driving on winding mountain roads? For bicycle tires, do you want your tires to perform well on a steel drum surface—or on a real road with a rider on board?
Rene Herse tires are the result of our real-road R&D. We optimize our tires by testing them on real roads, because we are convinced that this results in better tires for the riding we do. It’s totally natural that our tires ace the tests for which they are designed. If they didn’t, we’d continue developing them—until they did. In fact, that is why we test tires from other makers: to see how ours stack up. If our tires were slower on real roads than others, we would continue our R&D until they are at least as fast.
We started testing tires long before we made our own. In fact, we got into the tire business only because our testing showed that tires could be improved—if you developed them with the knowledge gained of real-road testing.
Of course, it would be nice to have an independent source confirm our test results. Unfortunately, nobody out there is testing tires on real roads with a rider on board. We’ve published our test protocol to inspire others, but, so far, there have been no takers. Testing on real roads is a lot of work—which is probably why no other tire maker is doing it. Absent any other choices, we do our own testing.
With our very first tire tests, way back in 2006, we had an independent observer at our testing, because we thought that people might question our results. They did—because the idea that wide tires could roll ultra-fast seemed just preposterous back then. In those early tests, our favorite tires didn’t win. In fact, the tires we were importing back then didn’t even score particularly well. That prompted a long journey of R&D to get where we are today. With the volume of testing we do, it’s not practical to have independent observers for all our tests. Especially since we can test only when there is no wind and constant temperature—something that’s impossible to schedule in advance.
Sending our tires to a lab that tests on a steel drum obviously doesn’t make sense, either. If we do that, we’ll start optimizing our tires like everybody else—to perform well on the steel drum, not on the road. That’s also why we decline to participate in tests that evaluate rolling resistance on steel drums.
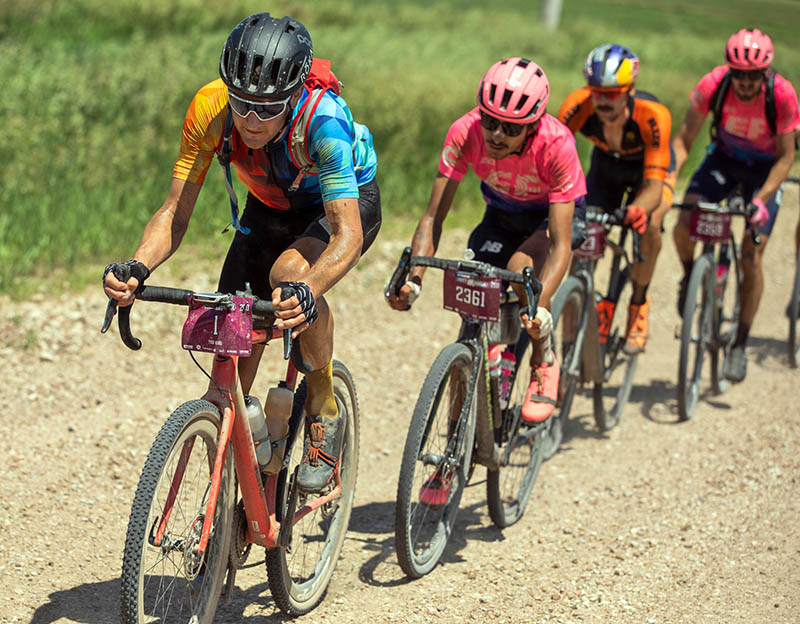
The goal of our testing is improve our tires and fine-tune them to the nth degree, not marketing. We don’t rely on test results to show the superiority of our products. For us, the proof is on the road, when people ride our tires. Whether they win races or just smile because their bike feels so alive—that’s when all the hard work becomes worthwhile. Our goal is not to ace a test, but to make the fastest, most comfortable, and most fun tires—for the real world we ride in.
Further Reading:
- Our book The All-Road Bike Revolution covers how tires work, what suspension losses are, and much more.
Photo credits: Arkland (Photo 2); Evo Magazine (Photo 3); Mercedes Benz (Photo 4); Ansel Dickey (Photo 10)