Why We Love Quick Releases — and Thru-Axles, too.
It wasn’t too long ago that every high-end bike was equipped with quick releases. (Track bikes were the rare exception.) Quick releases allow removing the wheels without tools. Good quick releases grip the dropouts tighter than nuts. Quick releases were considered so important for bicycles that the story of their invention is surrounded by myths.
These days, most quality bikes are equipped with thru-axles. Thru-axles thread into a hole in the frame or fork, eliminating the opening that you find at the bottom of dropouts, which allows the wheel to ‘drop out’ of the fork or frame. That’s why we talk about ‘forkends’ with thru-axle bikes, since they aren’t dropouts any longer.
Getting rid of the dropout eliminates the risk that the wheel comes out accidentally during hard braking—which is a real concern with disc brakes. Due to the location of the caliper, the front axle moves downward during hard braking—not only backward as it does with rim brakes. The only drawback of thru-axles is that most require tools to remove the wheels, but wider tires and tubeless sealants have made flat tires a rare occurrence these days. Few mainstream high-performance bikes are equipped with quick releases any longer.

The bikes I rode in Paris-Brest-Paris and in the Arkansas High Country Race have quick releases and dropouts. Am I retro? Or just trying to be different? Not at all!
I’ve talked about the slender fork blades of my bikes in the past, and how they offer suspension that improves comfort and speed (vibrations that absorb energy). Flexible fork blades do not work with disc brakes, because they cannot transmit the brake forces. With rim brakes, the brake forces are fed into the top portion of the fork, allowing the bottom to flex as the bike goes over bumps. (As an aside, the wire you see going into the fork blade is for the connector-less SON generator hub.)
There is nothing that prevents thru-axles to be used with rim brakes. So there must be another reason I run quick releases: For steel bikes, dropouts are much lighter. A quick release axle measures 9 mm (front) or 10 mm (rear) in diameter. That means the dropout can be much smaller than a thru-axle forkend that encloses a 12 mm axle. And since the dropout doesn’t need threads, it can also be a lot thinner.
The weight difference is significant: Rene Herse front dropouts (above) weigh 58 g for the pair. A set of steel forkends for a 12 mm thru-axle weighs twice as much. Multiply that by two, and you’ve added a quarter pound to the frame. And then imagine mating a beefy thru-axle forkend with my slender fork blades… That would look odd, so you probably want to beef up the fork blades, too. Which logically leads to a bigger steerer at the top of the fork, bigger frame tubes, and so on. Before you know it, you’ve got a ‘naked’ bikepacking bike that weighs 14 kg (30 lb), once you add pedals. You’ve also changed the ride characteristics with all those beefy tubes. Those bikes can be fun, but they don’t really claim to offer ultimate performance in the way the best carbon bikes do.
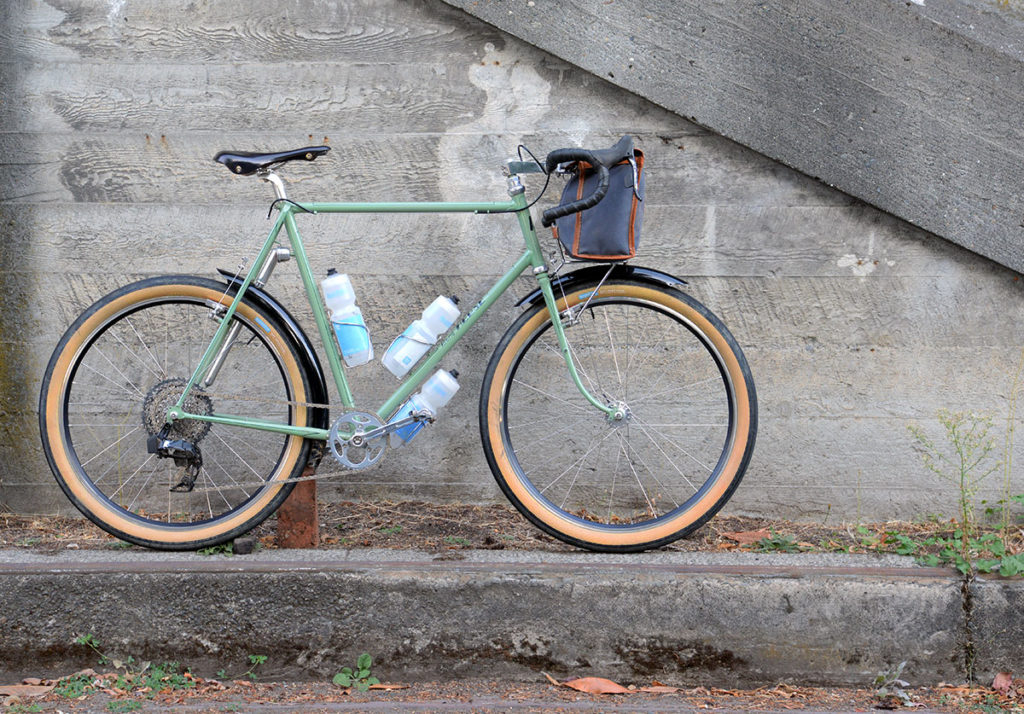
When I’m lining up for Paris-Brest-Paris or the Arkansas High Country Race, I want to be confident that my bike offers at least as much performance as all the others around me. I choose steel for many reasons: the afore-mentioned slender fork blades and their suspension, the ability to fine-tune the frame’s flex characteristics exactly to my liking, the ease of integrating lights, fenders, racks and other parts. All these things improve the bike’s performance, but I don’t want them to be offset by unnecessary weight and other compromises.
What it comes down to is this: A bike is a system where all parts work with each other. Steel is very dense and strong. You don’t need much to make a bicycle frame, but if you use more than necessary, the weight quickly balloons. That’s the reason why classic steel frames were so slender. Using these characteristics to their greatest advantage is the reason why my bike for the Arkansas High Country Race (above) weighs just 10.2 kg (22.5 lb) completely equipped. That includes wide tires, rack, generator hub, head- and taillights, pedals, three bottle cages—even the pump. (And those aero fender fairings.) Even with the bag, the bike is still below 10.5 kg (23 pounds). In theory, you could make a lighter bike from carbon, but in the real world nobody has managed to do this yet, once you factor in all those parts and the bags.
That doesn’t mean we’re turning our backs on modern materials: Rene Herse components use titanium bolts wherever this doesn’t compromise strength. There’s even a little carbon on this bike, in places where it makes sense. And the quick releases on my bike are superlight. (They are made by Tune in Germany and weigh just 39 g for the pair.) The result is a fully equipped all-road bike that weighs less than most carbon bikepacking bikes—and is customized exactly as I want it.
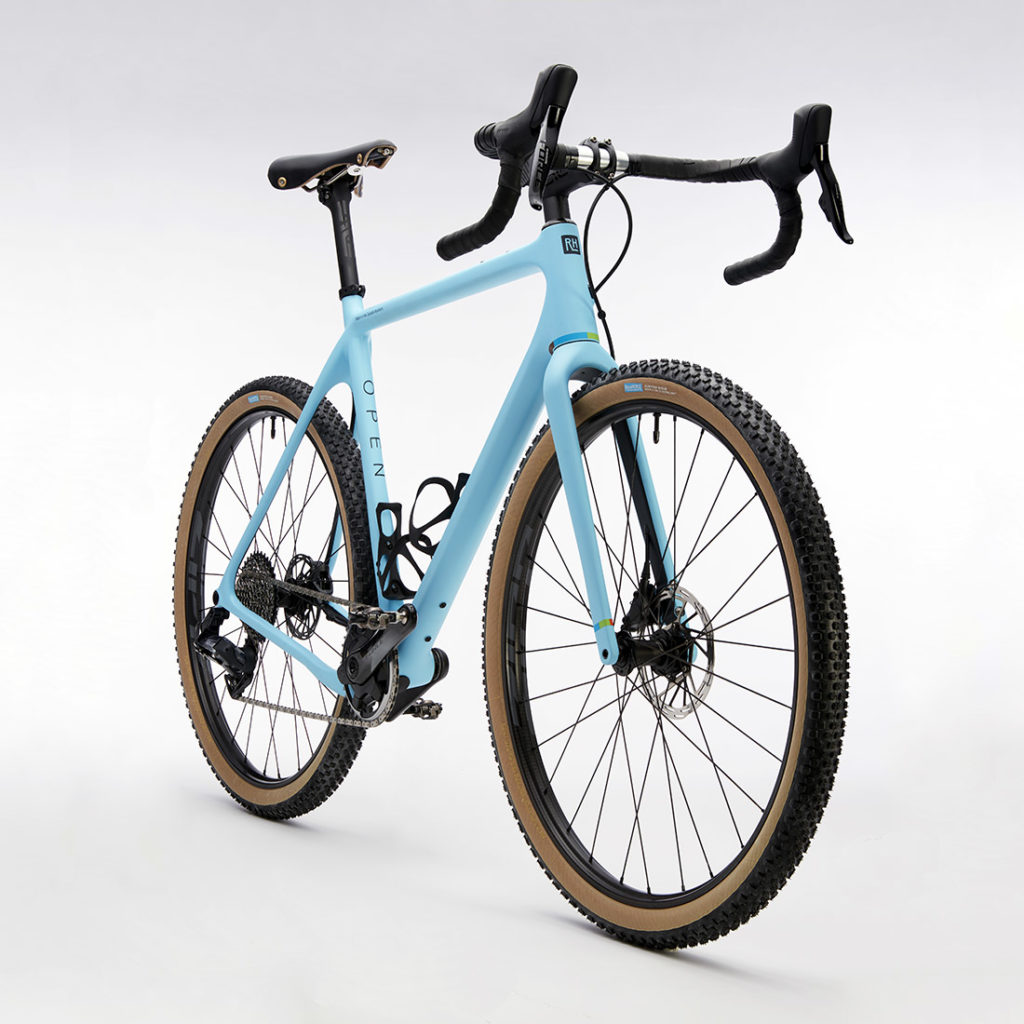
My OPEN × Rene Herse U.P.P.E.R. has thru-axles. Carbon is a totally different material from steel. For strength, you need a lot more volume of carbon than steel. But carbon is so light that the end result is (usually) a little lighter than steel. With carbon, you have to distribute stresses over a large area. That’s why superlight carbon frames need to be reinforced in all the places where a screw will be attached—think bottle cages, fork mounts, etc. (With steel, you just braze on an eyelet…) That’s one reason why carbon bikes don’t work well with cantilever brakes—or dropouts.
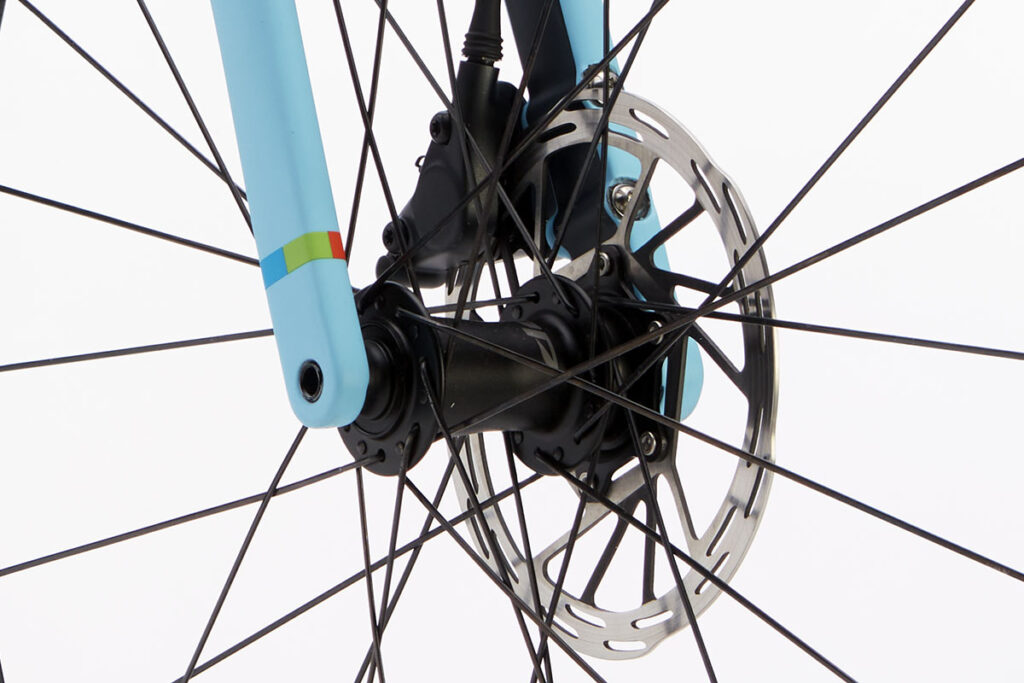
Since carbon fork blades are comparatively massive, a big hole for a 12 mm thru-axle actually saves weight compared to a smaller dropout. It’s not just that the bigger hole means less material… Dropouts need to be super-strong—they are open at the bottom—which means you have to make it from metal. With a thru-axle, all you need is a (light) insert in each carbon leg.
So it makes sense to use quick releases and rim brakes on steel bikes, but for carbon, disc brakes and thru-axles are the logical choice. The same applies to other parts of the bike. Take bottom brackets, for example. On a carbon frame, the BB area is massive, and making a big hole for an oversized spindle is a no-brainer. On a steel bike, that oversized spindle needs to be surrounded by a larger bottom bracket shell—making it much heavier. (The BB shell is already the heaviest part of the frame.) The same applies to cranks—carbon cranks work much better with oversized spindles, but aluminum cranks get very heavy when you beef them up to surround the huge spindle. (Unless you make the aluminum cranks hollow, but a recent recall of over two million cranks shows that this is not as easy as it may appear at first.)
Bikes are complex systems, where all parts interact with each other—and with the rider. If you’re curious about all this and more, check out our book The All-Road Revolution.
Further Reading:
- The All-Road Revolution is our book that explains how bicycle really work.
- Our favorite quick releases are made by Tune in Germany. We’ve been out of stock, but more are on the way and should arrive next week.