Tire Testing: Lab vs Real-Road
In discussions of supple tires, you sometimes hear comments along the lines of: “If wide tires are so great, why don’t they score at the very top in lab tests?” That’s a good question, and it goes to the root of how to test things: If tests don’t replicate the real world, they aren’t of much use.
We probably shouldn’t complain: In most lab tests, Rene Herse tires have lower rolling resistance than other comparable tires:
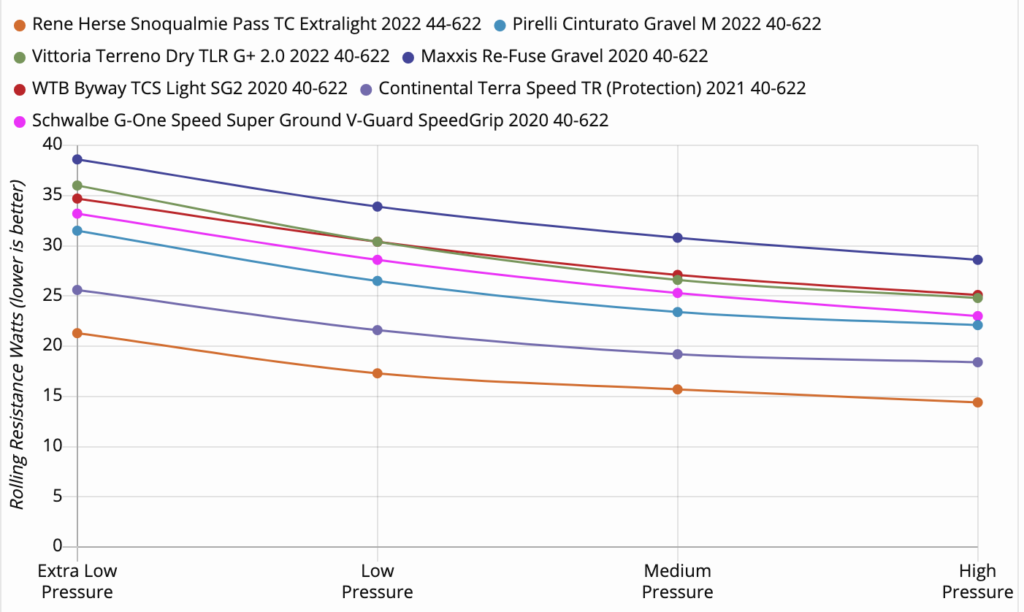
Above are lab test results of gravel tires, showing our Snoqualmie Pass 700C x 44 fastest by quite a margin (orange line). But that doesn’t mean that current lab tests are reliable indicators of tire performance. They don’t capture the entire story when it comes to tire performance. This can be misleading in many ways, especially when you compare wide and narrow tires. In lab tests, narrow tires usually score better—but they don’t in the real world. Here’s why:
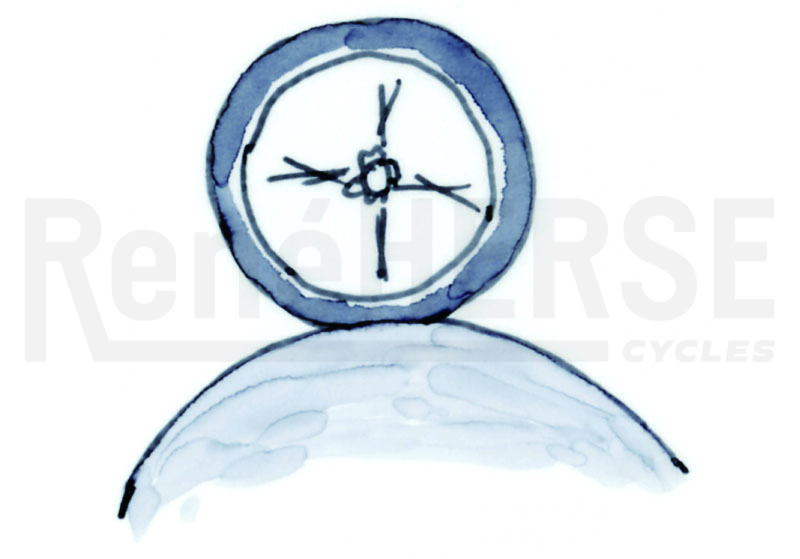
Lab Tests are usually done on a steel drum. It’s a relatively simple test: You measure how much power it takes to spin the empty drum. Then you add a wheel with a tire, and you measure the power again. The extra power is the rolling resistance of the tire. (There’s also a little resistance in the hub bearings, but that’s negligible.)
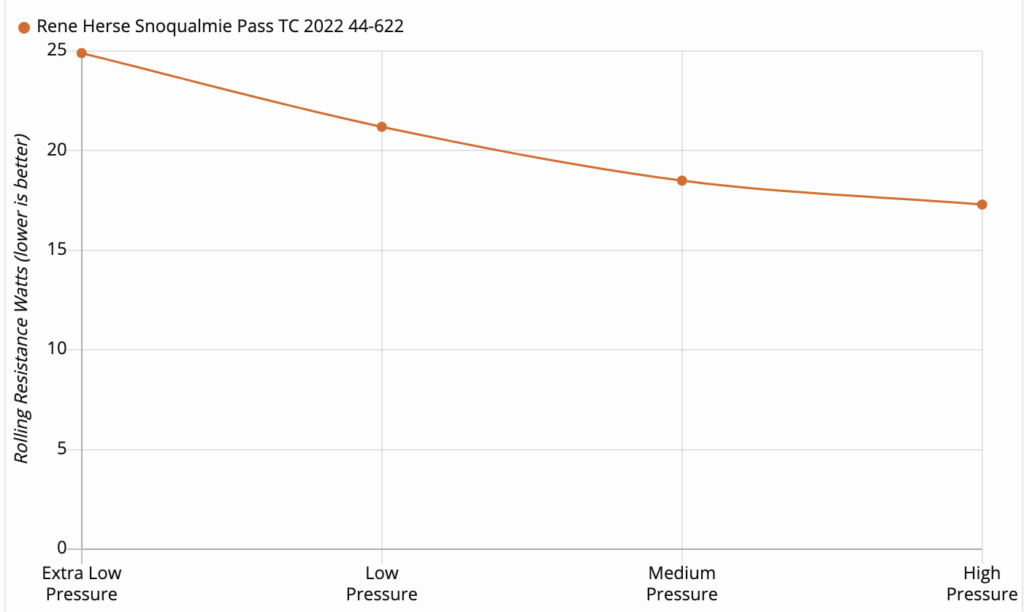
Above are the results of a drum test of our Snoqualmie Pass 700C x 44 mm tires (Standard casing). You see how the rolling resistance goes down as pressure goes up. How can we make this tire even faster? It looks like a no-brainer: Increasing the tire pressure further will make the tire even faster.
That is, until you run into the Snoqualmie’s maximum pressure rating of 75 psi (5.2 bar). Want to go even higher? Easy—just make the tire narrower. With the same casing, a 28 mm-wide Chinook Pass can be inflated all the way to 105 psi (7.4 bar). It’s obvious that if you compare the 44 mm tire with the 28 mm tire, both at max. pressure, the narrower tire will be faster—at least on the steel drum.
You see where this is heading: Right back to the last century, when racers gritted their teeth as their bikes chattered across the road on 20 mm tires inflated to 125 psi (8.6 bar) or more. But these days even ProTour racers roll on 25 or 28 mm-wide tires and rarely inflate them to more than 75 psi (5.2 bar). What do these racers know that the lab tests don’t show?
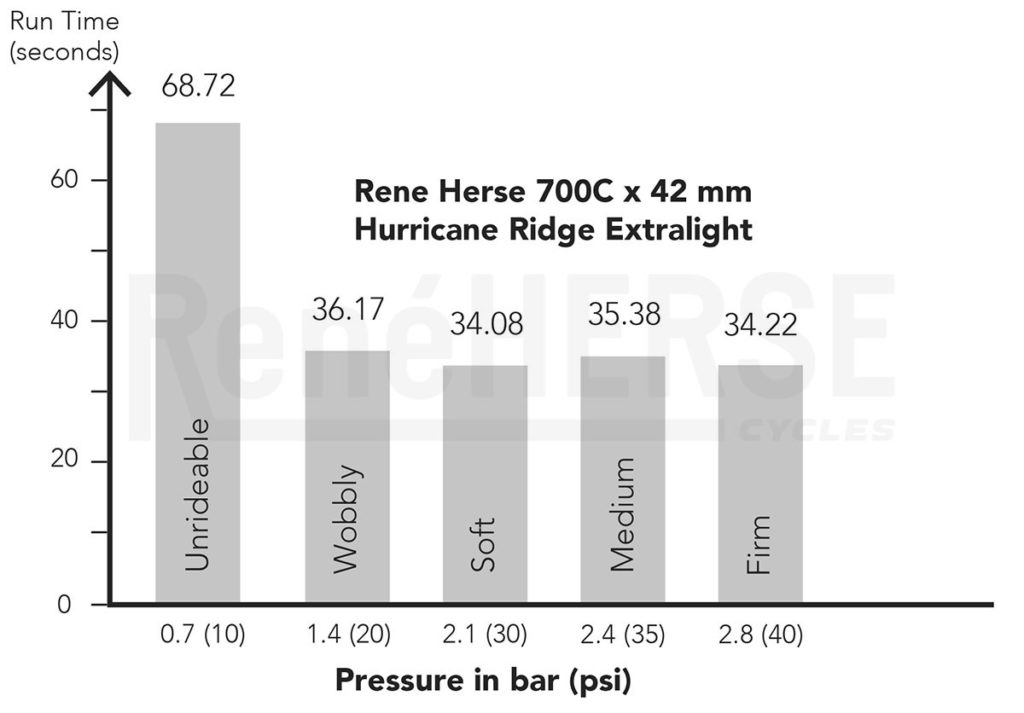
Testing supple tires on real roads, with a rider on the bike, shows that higher pressures do not roll faster—as long as you keep the tires inflated enough that the bike can be ridden and steered normally. Above you see data for 42 mm tires: They roll at the same speed at 30 psi (2.1 bar) and at 40 psi (2.8 bar). Why aren’t the tires faster at ‘Firm’ pressure than at ‘Soft’ pressure?
Let’s look at how tire pressure affects performance in the real world:
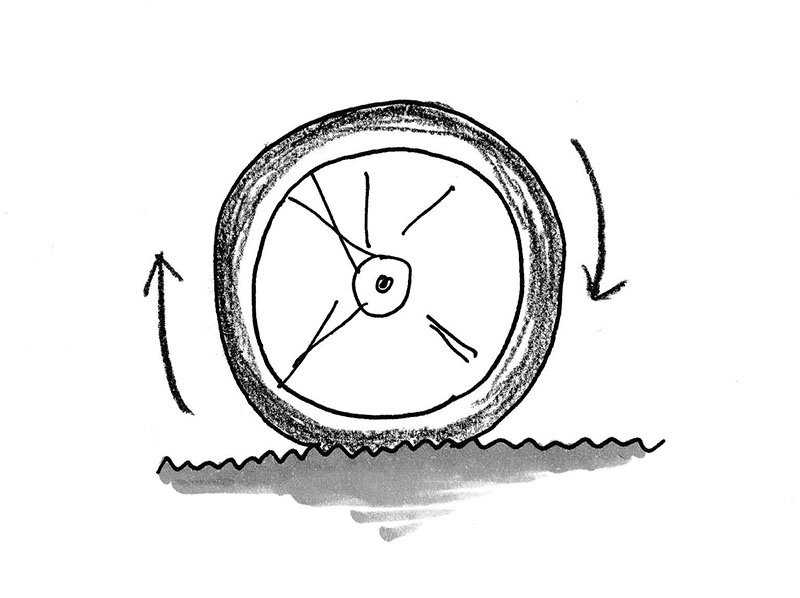
Higher pressure means the tire flexes less. Flexing the tire takes energy. (Imagine squeezing a tennis ball.) At higher pressure, the tire absorbs less energy as it deforms where it touches the ground. The technical term for this is hysteresis loss. This is why high pressures score better in the lab.
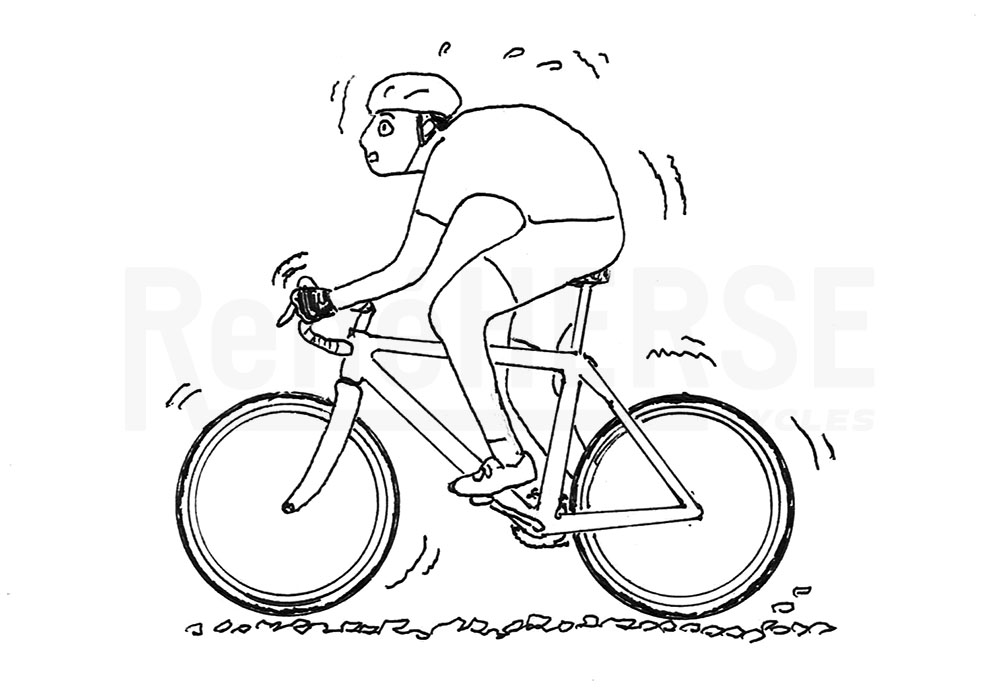
In the real world, it’s not that simple. Higher pressures transmit more vibrations. These vibrations slow the bike down, mostly due to friction between the rider’s body tissues. That’s right: What riders experience as discomfort is in fact friction inside their bodies. The technical term for this is suspension loss—sometimes also called ‘vibration loss.’
Lab tests on steel drums don’t measure this suspension loss. Even if you cover the drum with a rough pattern, there’s nowhere to dissipate the vibration energy. Without a rider (or something to simulate the rider’s body tissues), you are missing the most important part of the suspension loss.
Both factors together determine how fast your bike rolls on different tires. If we express this as a formula, it looks like this:
Tire Resistance = Hysteresis Loss + Suspension Loss
In the real world, these two factors cancel each other, at least with supple high-performance tires. Running higher pressure doesn’t make you faster.
A narrow tire (at high pressure) has low hysteresis loss and high suspension loss.
A wide tire (at low pressure) has high hysteresis loss and low suspension loss.
The end result is the same, as far as speed is concerned. (The difference in comfort is another story.) This isn’t just theory, but something we’ve found in numerous tests. Here is a recent example:

Remember how the lab test suggested that a 28 mm tire (at higher pressure), would be much faster than our 44 mm Snoqualmie Pass? Above are real-road test results of our Snoqualmie (44 mm) and Chinook Pass (28 mm) tires. We ran the 28s at more than twice the pressure (65 vs 30 psi). And yet there’s no speed difference between the 44 mm and the 28 mm tires.
We did multiple test runs to make sure that we were measuring tire performance, and not some other factor, like a small change in rider position. (We test only on days with no wind and constant temperature, and we’ve confirmed in a wind tunnel that our tester can maintain the same position from one run to the next. We always perform a statistical analysis to make sure that we don’t have excess ‘noise’ in the data.)
So we’ve seen that drum tests don’t measure suspension loss, and therefore falsely suggest that higher pressures roll faster. And since only narrow tires can be inflated to ultra-high pressures, lab tests show narrow tires rolling fastest. In the real world, the increased vibrations cancel any gains from higher pressures, at least for supple high-performance tires.
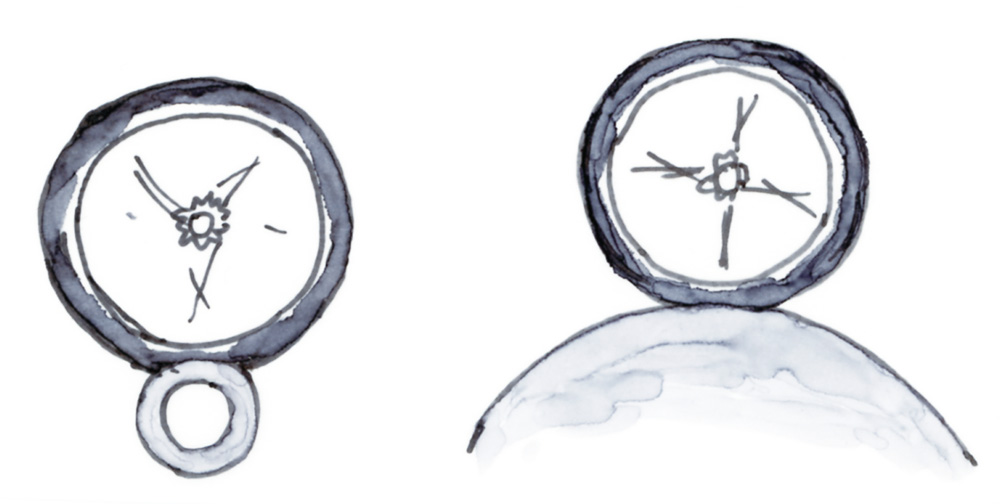
There’s another problem with lab tests on drums: The drum is convex, and it digs into the tire more than a flat road surface. This flexes the tire more, and it increases its rolling resistance. That alone wouldn’t be a huge problem, if it affected all tires the same. But it doesn’t: Supple tires deflect more than stiff tires. That means they have a disadvantage on the steel drum that doesn’t exist in the real world. Even if drum tests show supple tires being faster, they won’t show the full advantage you get from running supple tires.
The problem of the convex drum applies even more to knobby tires, since the drum concentrates the pressure on a small area of the tire tread, rather than spread it over multiple knobs.
A small drum will penalize supple tires and knobbies more than a large drum. From what I’ve heard from tire engineers, you need a drum that’s at least 1.8 m (6 ft) in diameter if you want to reduce this effect to the point where it’s no longer a problem. A drum that large would be hugely expensive, so everybody measures on smaller drums.
Let’s look at how this plays out in the data:
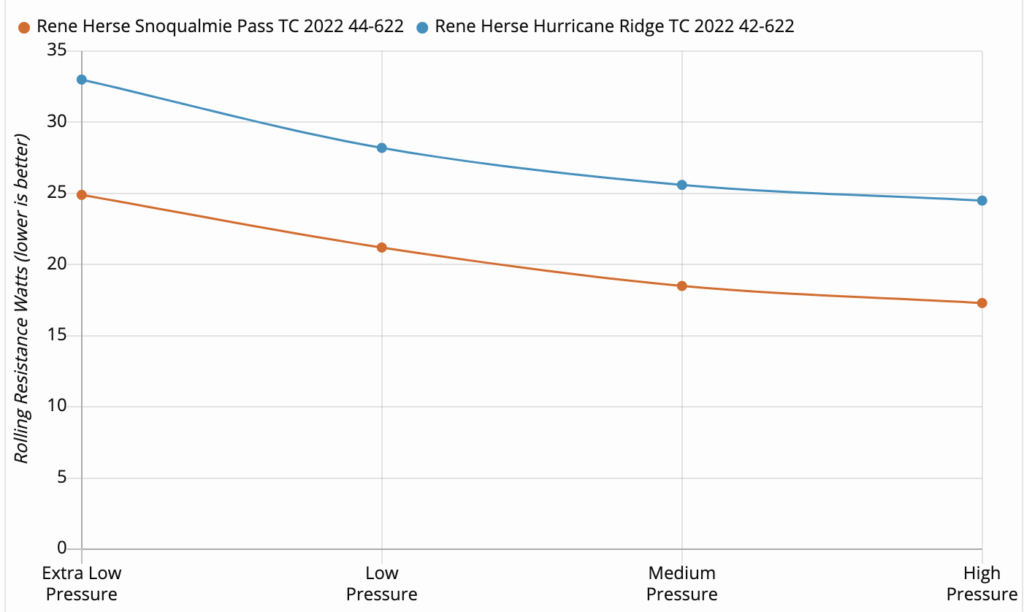
Above you see drum test data for our 700C x 42 mm Hurricane Ridge knobbies (top) and our smooth 700C x 44 mm Snoqualmie Pass (bottom). It appears that the knobbies roll much slower. Based on the above, you’d want to run smooth tires whenever you can. You’d also want some ‘intermediate’ knobbies that aren’t as aggressive, since they should be faster for all those times when you need a little more traction, but full knobs seem like overkill.
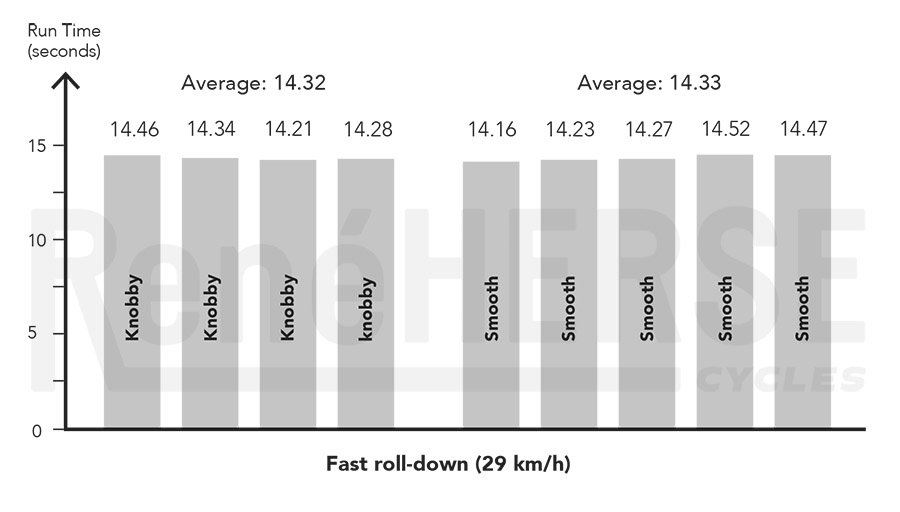
Testing the same tires on real roads, with a rider, there’s no difference between the knobbies and the smooth tires. The knobbies spread the load over so many knobs that they don’t squirm or flex. The knobs don’t slow you down. That’s why there’s no reason to make a semi-slick or an intermediate tire with shallower knobs, as these would not roll any faster. (We’ve tested that, just in case, with shallow-knob prototype tires that Peter Weigle, the famous builder, shaved down for us.)
Of course, not all knobbies roll that fast. Our Rene Herse dual-purpose knobbies have computer-optimized knob shapes, sizes and distribution to prevent the squirm and folding over that you get with smaller knobs and less optimized shapes.
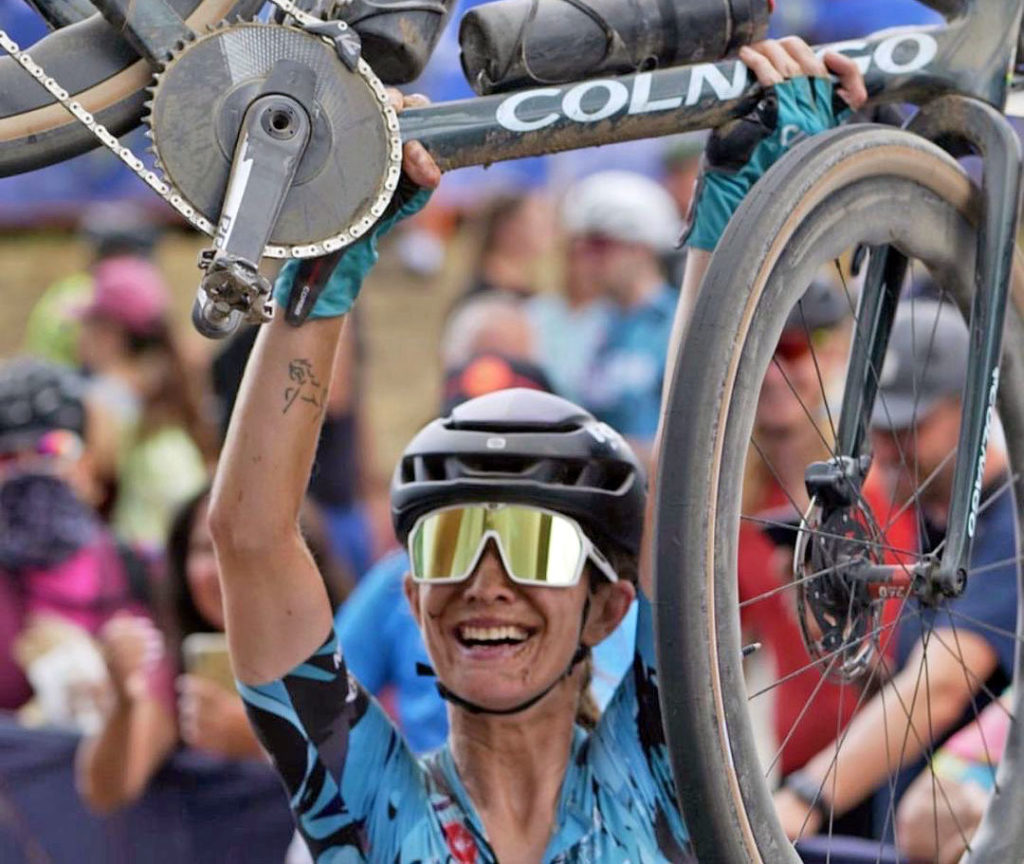
Conclusion
Lab tests on steel drums have three major issues when it comes to assessing the performance of tires:
- They suggest that high pressures (and hence narrow tires) roll faster.
- They concentrate pressure on a small area of the tire, so knobby tires perform worse than they do in the real world.
- They underestimate the advantage you get from supple tires.
Testing Rene Herse tires on steel drums doesn’t make much sense: After all, we developed our tires when we realized that steel drums don’t replicate real-world conditions. If steel drum tests were the last word in testing rolling resistance, we’d all still be riding 20 mm tires, and the ‘All-Road Bike Revolution’ wouldn’t have happened at all.
Of course, all theory and testing have to prove themselves in the real world. How do wide tires fare in actual races and timed events? I already mentioned that pro racers have moved to wider tires and lower pressures, and their speeds haven’t gone down. Riders like Lauren de Crescenzo (above) have won many gravel races on Rene Herse tires that were much wider than the tires of their competitors. And in the Oregon Outback, I set an FKT (Fastest Known Time) on 54 mm tires inflated to just 19 psi (1.3 bar). Looking at my tracker after the ride, it was clear that there was no loss in speed on the paved sections of the course.
I think it’s fair to say that this issue is settled: Higher pressures don’t make you faster. And lab tests on steel drums don’t tell the whole story of how tires perform in the real world. It’s more difficult to test tires on real roads, with a rider, but it’s the only way to get meaningful results that help us develop faster and more comfortable tires.
Further Reading:
- ‘How We Test Tires’ explains how we control variables like wind, temperature and rider position in our real-road tests.
- Some results of Bicycle Quarterly’s tire tests.
- The All-Road Bike Revolution, our book that explains how bicycles work in the real world.
Credits: Steel drum test data from www.bicyclerollingresistance.com; Unbound Photo: Andy Chasteen